Safety & Regulations | Hazard Protection Protocols | Hazard Protection | Petrochemical Industry | Petrochemical Industry Explosions
How Likely Are Explosions in the Petrochemical Industry?
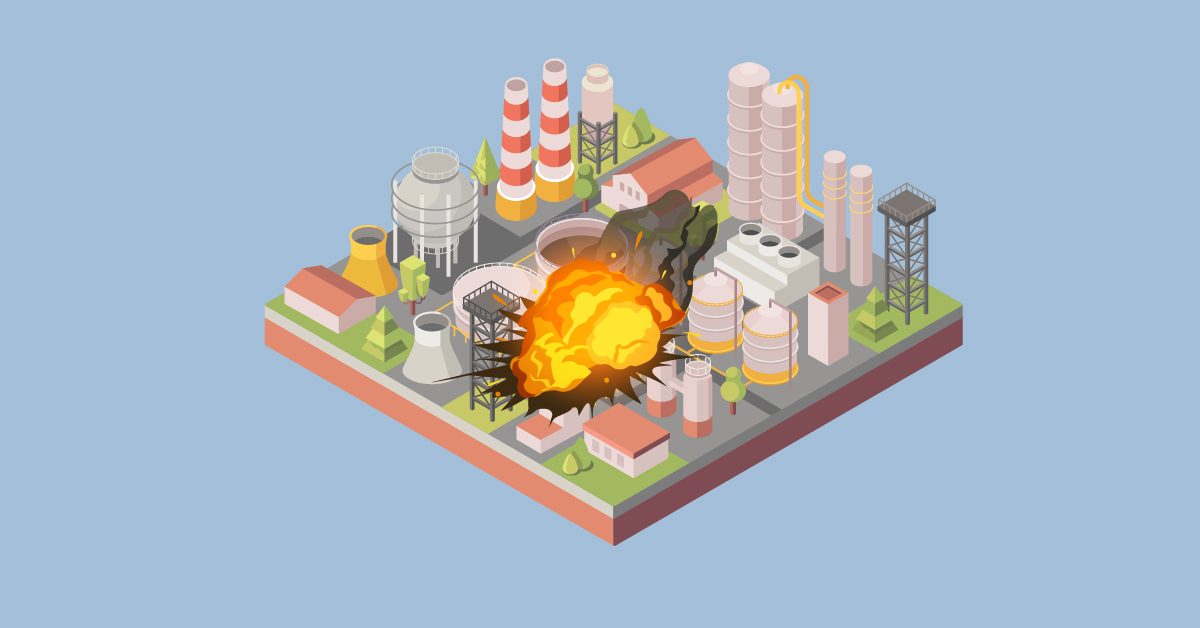

Safety of the Employees and Equipment
Workers in the petrochemical industry are subject to numerous risks, including chemical leaks, fires, and explosions. These are in addition to the risks common throughout the manufacturing industry, such as machinery malfunctions and falls.
In 2020, the petroleum industry had 1.2 recordable work-related injury and illness incidents per 100 workers and three fatalities. Considering the risks, the injury rate is relatively low. And while events such as explosions at petrochemical plants can be devastating, they tend to be rare.However, explosions in the petrochemical industry do happen, and they often occur on sites that have experienced safety lapses in the past. Below, we'll look at how these explosions occur and how petrochemical facilities can best protect their workers.
What Causes Explosions at Petrochemical Facilities?
While petrochemicals are used in everything from plastics to cosmetics, refining them can be dangerous. Humans exposed to petrochemicals may suffer from organ damage and cancer, which is why the industry has gone to great lengths to curb any emissions of toxic substances and install safety measures when building petrochemical facilities.
Despite the inherent danger of working with volatile chemicals under immense amounts of pressure, the most common causes of petrochemical facility explosions are preventable. While natural disasters, such as lightning strikes, can also cause explosions at petrochemical facilities, most accidents are related to equipment malfunctions and human error (including poor safety responses). Other causes include maintenance issues, equipment deterioration, and operator errors.
A 2016 study showed that this is common across manufacturing industries. Out of 96 process safety incidents they studied, 60% resulted in explosions, and most were influenced by unsafe work practices or deficiencies in operating procedures.
Despite the severity of the blasts that have occurred, the overall likelihood of an explosion at a petrochemical plant is still relatively low. But the chances go up when equipment safety management and personnel safety training are poor.
How to Prevent Chemical Plant Explosions
OSHA mandates that all manufacturing facilities create a safe work environment for employees and eliminate known hazards. It also requires chemical plants to:
- Commit to regular checks and inspections of work conditions and equipment
- Provide employees with protective equipment
- Schedule regular maintenance on all equipment
- Notify workers and site visitors of any hazards
- Provide safety training for workers and regularly review and update safety regulations
- Record exposures, injuries, and accidents
- Develop and train workers on appropriate emergency plans
OSHA violations are a common predictor of petrochemical plant explosions. And many of the U.S.'s most notorious incidents were later found to be the result of "willful violations" of OSHA protocols, including:
- The October 23, 1989 accident that killed 23 workers and injured over 130 others in Texas
- The October 6, 2005, propylene explosion in Texas, that resulted in 12 injuries (including four severe enough to require hospitalization) and a subsequent fire that burned for five days
- The November 27, 2020 blast at a plant in Texas that injured three workers, caused widespread damage, and required the evacuation of 50,000 nearby residents.
In other words, the best way to prevent explosions is to learn from past mistakes, institute strict safety protocols, and ensure employees understand how to implement them.
How to Protect Your Team in the Event of an Explosion
Despite the inherent risks involved in the petrochemical industry, there are straightforward steps companies can take to protect their people and property from explosions. These include formulating solid hazard protocols, training workers to respond to emergencies, and providing a safe space if a blast cannot be contained.
Blast Resistant Buildings
Regardless of the cause of a petrochemical blast, a blast resistant building can help save lives on a worksite. Blast resistant buildings are a cost-effective way to give workers a safe haven and the peace of mind to know they're protected in case of an explosion. They also allow companies to reduce their liability and increase their safety compliance.
While the American Petroleum Institute's API 752 / 753 lay out recommended practices for the construction and installation of blast-resistant buildings to protect their occupants, they don't mandate materials. At RedGuard, we use steel because of its superior ability to withstand the shockwave of an explosion while protecting the people inside. Steel has the superior ductility and tensile strength to withstand blasts up to 9.9 psi. We can be sure of it since our modules are blast tested by third-party engineers.
Hazard Control Protocols
Even if employees have the tools to stay safe, employers must develop hazard control programs to ensure they know how to use them. These programs contain the procedures required to control exposure to all worksite risks and ways of monitoring their effectiveness.
As we've seen, blasts often occur due to deficient safety procedures. It stands to reason that by improving safety protocols, workers will be empowered to keep themselves safe and develop the skills and awareness necessary to prevent some incidents altogether.
Team Training
Safety protocols are only as good as the training used to implement them, so it's essential to ensure your team knows what to do in the event of an explosion. This requires developing a formal process safety training program under the direction of a supervising engineer.
Team training should include elements such as developing a familiarity with the hazard control protocols and emergency plans, instructions on how to use safety equipment, information on how to report incidents, and emergency plans. It's also vital that safety training be relevant, comprehensive, and ongoing.
Blast Resistant Buildings for Petrochemical Facilities
Petrochemical facilities have inherent dangers due to the volatile materials they process. And while explosions are rare, they do occur, and they can be devastating.
Preventing explosions requires a rigorous safety program and training your team to abide by it. And when the worst occurs, having a blast resistant building on site can protect your people from the most serious harm.
Contact us if you're interested in learning more about RedGuard's safety-tested steel blast resistant buildings.
RedGuard Sales & Marketing
The RedGuard sales and marketing team curates and writes on a variety of topics regarding blast-resistance and modular buildings. To inquire about any of the topics you read about on our blog, connect with us.