Best Practices | Safety and Regulations | Petrochemical Industry Explosions
How RedGuard Blast Tests Compare to Plant Explosions
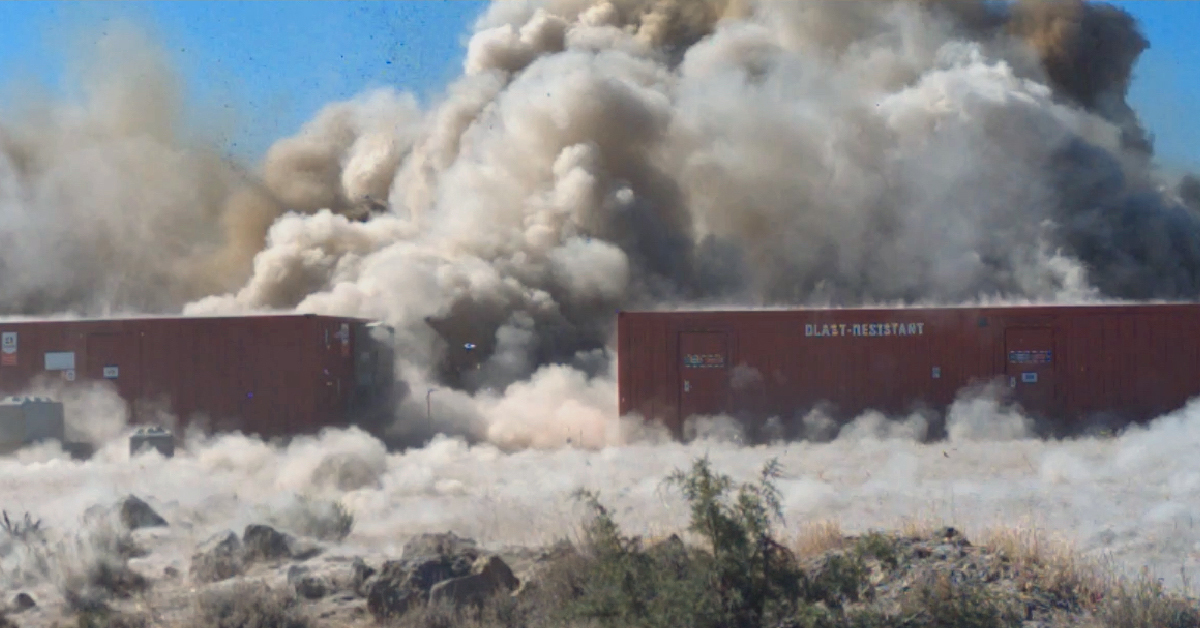

Performing a real-world blast test on a blast resistant building is one of the best ways to alleviate concerns about how a structure will react to a real disaster. No computer model can compare to seeing a building survive a blast with your own eyes.
When plant explosions occur, they can be damaging and deadly. Not only can blasts do immediate damage to people and property with the resulting pressure, but they can also lead to high temperatures, fatal fires, flying shrapnel, and chemical leaks. From petrochemical plants to construction sites, faulty equipment and natural disasters can cause explosions even when safety procedures are in place.
Below, we'll examine the importance of not only having a blast resistant building on work sites but ensuring the company that makes the structure has thoroughly tested their buildings and can back up claims about the strength of the blasts they can handle.
How RedGuard Conducts Blast Tests
RedGuard is fully transparent about the results of their blast tests and makes all resulting information (including blast test video) available to potential customers. Complete transparency helps RedGuard customers understand the protection they're getting before making a purchase.
Blast test #1
One early RedGuard blast test used a module built according to standard specifications with tube steel stiffeners strengthening roof and wall panels. Using 1250 pounds of high-explosive ammonium nitrate at a standoff distance of 110 feet, RedGuard created an explosion with a strength of 10 psi that lasted 25 msec. Inside was a desk, computer, and test dummy designed to gauge the impact on the structure and the people and property.
The results were encouraging as the building, and its contents survived without structural damage, shifting less than two inches due to the blast.
Blast test #2
In a more recent blast test on August 11, 2020, three different blast resistant buildings were placed on an arc around a 6,000-pound ammonium nitrate/fuel oil (ANFO) charge. The test involved one anchored building and two unanchored buildings (in addition to a wooden trailer and job site truck for comparison).
All of RedGuard's blast resistant buildings survived the blast while the wooden trailer collapsed. Some non-structural damage was recorded in the flooring and interior finishing. Still, the buildings satisfied the requirement for a Low Damage Level from the American Society of Civil Engineers' "Design of Blast-Resistant Buildings in Petrochemical Facilities."
What Happens When an Explosion Occurs?
Unfortunately, we know quite a bit about the damage that can occur due to plant explosions, especially in the petrochemical industry. In Texas alone, there have been six plant explosions since 2019. Some were ignited by small fires, while others were the result of malfunctioning equipment. In most cases, workers suffered burns, chemical inhalation injuries, and pressure blast trauma - some resulted in fatalities.
For example, a St. Patrick's Day 2019 plant explosion occurred after two tanks caught fire, which then spread to neighboring storage tanks containing toluene, naphtha, and xylene. The fire took three days to extinguish fully. There were no fatalities, but the incident caused 20 injuries and complaints of breathing issues, nose bleeds, and headaches from workers and nearby residents who were forced to shelter in place due to contaminated air. This required the company to offer a massive compensation package to all those affected by both long and short-term health issues, and the chemicals still linger in the Houston ship channel, which connects to the Gulf of Mexico.
Even in cases where chemicals cause widespread damage, a thorough safety program that involves the placement of blast resistant buildings can help prevent some casualties. And a blast resistant control room can help employees get initial explosions under control safely before they escalate to significant disasters.
How RedGuard's Blast Tests Measure Up to Real-Life Explosions
A blast test can replicate the power of some, but not all, explosions. And it can't adjust for the reactions of people on site or give much insight into the long-term ramifications of a chemical plant explosion. Still, knowing about the safety features offered by these buildings can make employees more safety conscious and give them the protection they need to maintain the presence of mind required to control fires and chemical leaks before they spiral out of control.
Without a safe place to shelter and knowledge of how to access it, it's only fair to expect employees to move as far away from an accident as possible without leaving anyone to contain it. In other words, there are psychological considerations to keep in mind when it comes to building an on-site safety plan. RedGuard's blast resistant buildings are modular. Still, they are built like permanent buildings, providing a psychological advantage to those who feel safer in a structure that doesn't look or feel portable.
A worksite that takes safety seriously is more likely to retain experienced workers who know how to keep a cool head in an emergency.
It's important to note that while RedGuard's blast tests placed structures less than 200 feet away from the detonation zone, the most recent test used 6000 pounds of ammonium nitrate. For comparison, the most recent U.S. disaster involving ammonium nitrate occurred on January 31, 2022, destroying a fertilizer plant in Winston-Salem, North Carolina. The plant housed 2000 tons of ammonium nitrate (or 4.5 million pounds) overall (though "only" 600 tons, or 1.2 million pounds, ignited during the accident).
Plant Explosions FAQs
How likely is a chemical plant explosion?
Major incidents are relatively rare, considering the number of operational chemical plants. But they do still happen, and they can be devastating.
Companies that take worker and plant protection seriously will have thorough safety plans, a record of following protocols, good maintenance standards, and blast protection. They will be open about how they keep sites compliant and workers safe from potential incidents.
How can I protect my team from a potential explosion?
As a safety manager, staying up to date with compliance measures, including employee training, is the best way to protect people and property from chemical fires and blasts.
In addition to OSHA safety requirements for workers, safety managers should abide by OSHA's Process Safety Management of Highly Hazardous Chemicals (PSM) standards to ensure the proper storage of process equipment in blast-resistant structures.
What requirements must a blast resistant building have to protect my team?
After getting a facility siting study, plant and safety managers will have a better idea of the risks at their unique facility so they can manage risks. RedGuard can aid in performing these studies and other risk analyses and customize a building to a site's specifications.
It's crucial to hire a company that can custom-build blast resistant buildings with the necessary quality controls, proof of blast tests, and flexible design elements that fit into their unique safety plans. A good blast resistant building company will have specialists who know the most up-to-date regulations and building codes to ensure maximum protection and compliance and can assist in training your employees to use the building to its full benefit.
Prevent Plant Explosions with RedGuard's Steel, Blast-Tested Buildings
RedGuard blast resistant buildings come with proof of efficacy, expertise in compliance, and years of experience working with a myriad of high-risk industries.
Read more about how RedGuard can help protect your petrochemical facility and check out our blast test results to see our buildings in action.RedGuard Sales & Marketing
The RedGuard sales and marketing team curates and writes on a variety of topics regarding blast-resistance and modular buildings. To inquire about any of the topics you read about on our blog, connect with us.