Safety & Regulations | Best Practices | Terminology
What Is A Blast Test?
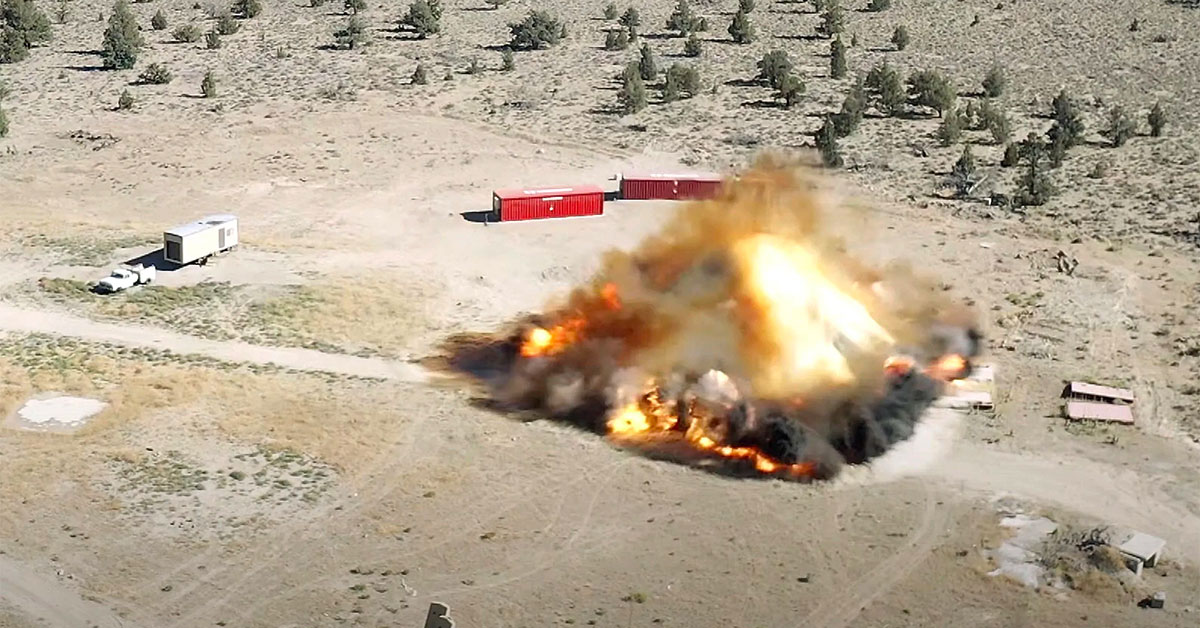

We understand the lengths that our customers go through to keep themselves and their team safe. We also know that sometimes the terminology around blast resistant buildings and their blast ratings can be confusing. Some readers might actually be reading this from the comfort of a BRB and wonder how it was determined to be a safe space.
RedGuard has always been transparent with the findings of the blast tests on our buildings. This article will delve into what a blast test is, how it’s performed, and why. And we’ll relate that to the terminology that you might see around these buildings, and our latest test.
What is a blast test?
A blast test is a staged explosion, usually performed to test the effect of a blast wave on structures that will be occupied in hazardous areas. They can also be staged to test other products like body armor, buildings that store and protect equipment from hazards, and a range of other materials and equipment that are used or stored in hazardous areas.
Companies that manufacture and design blast-resistant modular buildings will employ the services of an engineering firm to create an explosion large enough to simulate the type and strength of the blast that they are protecting against. (Occasionally, a blast test will be completed by an internal engineering team - more on that later.)
Military or defense contractors and governmental organizations would also be candidates for testing explosions, for example, to prove the efficacy of a structure or product against improvised explosive devices, or IEDs.
Do all modular building manufacturers do blast testing?
No, some modular structures are not meant to be placed in hazardous areas, so no blast tests are performed. In fact, not even all manufacturers of blast-resistant buildings perform blast tests. They may simply rely on the complex mathematical models that predict how a building will respond to an explosion. Blast testing is not a requirement.
Then, there are other manufacturers who do blast testing, but are not forthcoming with their test results.
So, while a blast test is not a requirement of blast-resistant building manufacturers, you should make sure it’s on your list of requirements. When considering options for a blast-resistant building, it’s best to find a supplier who is willing to share their blast test results, and who has worked with a third-party engineering firm to perform the test.
Where are blast tests performed?
Blast tests are typically done in a remote, wide-open area to avoid populated areas where injuries would be likely. They are careful to avoid areas near utilities, public roads, or structures that are not part of the test.
They are performed in areas where several hundred acres are available so that the large footprint of a blast wave can be measured and so that structures can be placed at various intervals from the explosion. Though remote, it is important that the activities can be closely monitored.
How big is the explosion during a blast test?
The size of the explosion is chosen by the company that is hiring the test and would be dependent on what and why they are testing.
As an example, our most recent RedGuard blast test employed 6,000 pounds of ammonium nitrate/fuel oil (ANFO), and buildings in the test were placed at standoff distances of 173 feet and 193 feet. Our company’s previous blast test used 1,250 pounds of ANFO and a standoff distance of 110 feet.
We opted for a higher charge weight and a larger standoff distance for this test to increase the duration of the pressure wave on the buildings. It’s difficult to replicate a vapor cloud explosion, like those that would occur due to accidents from fluid catalytic cracking for example, where extreme temperatures or volatile substances would be present. So, instead of hitting the buildings with lower pressures and longer durations, the structures are exposed to higher pressures and shorter durations, which allows the results to be correlated based on member capacity and measured/observed performance.
The amount of ANFO in a blast test may not clarify for some the size of the explosion. To understand the magnitude of the test explosion, we draw a careful comparison to the tragic event at the Alfred P. Murrah Federal Building in Oklahoma City in 1995, when terrorists detonated a bomb that used 4,000 pounds of ANFO and other materials in a truck parked beside the building.
Few people can forget the sight of the remains of the crumbling building after such an unfortunate and deadly event. It’s important to note there are differences in the materials used in that real-world event and the events that engineering firms stage. Still, you can be certain that the blasts manufactured to test safe structures are themselves dangerous blast events. Companies performing these tests use safety precautions to ensure that their team observing and working the test are protected.
The RedGuard blast test explosion produced a blast load ranging from 23.5 psi on the front of a building to 4.7 psi on the rear of the building. These numbers are the pressure, measured in psi, or pounds per square inch. Measurements are typically taken from every side of each structure placed in the test.
You may have also seen measurements applied to buildings that express the duration of a blast, measured in milliseconds. When analyzed in those terms, the free-field pressure was 9.9 psi for 24 milliseconds.
Who performs a blast test?
As mentioned previously, the blast test should be performed by an engineering firm that specializes in blast resistance, hazards/risk management, security, or safety engineering and design. To ensure that the engineers performing the test have no conflicts of interest, many companies stand behind their choice to employ an independent third-party engineering firm.
The conflict of interest that could be present with an internal engineering team rests on the fact that those engineers have an interest in the performance of the structure or other product being tested. While we hope that the engineers employed by a manufacturer would not intentionally affect the test results, there are unintentional ways that a test could be adversely affected. When a company performing a blast test is also selling a product from which they will directly profit, a conflict of interest could result in a company’s failure to act in their customers’ best interest.
There’s no standard protocol making testing by a third party a requirement, but it makes sense to avoid conflicts of interest when lives are at stake.
What happens after the test?
After the blast test is performed, evaluations begin. Before the test explosion, they will have taken many pictures of the structures, both internally and externally, and set up instruments and gauges, depending on what they are testing for. After the explosion, before anything else is done, they will take “after” pictures to compare and look for building and component response.
Some of the data could come from accelerometers, pressure gauges, temperature gauges, and anthropomorphic test devices, or ATDs. An ATD, more commonly known as a crash test dummy, records force and acceleration data to determine if injuries are likely.
The engineers look at key data points and instrumentation levels from the test. They will assess whether or not there is damage to the structures (the response) or to any of the ATDs that were placed in the buildings. They will note if the structure moved from its base and if the explosion damaged the walls or support beams. They will observe non-structural component response, like if objects inside the structure moved during the blast. And they will watch video of the blast event to observe the amount of dynamic load transfer, or flex, in the building’s steel walls.
What is dynamic load transfer?
Dynamic load transfer, or flex, in a blast resistant building refers to how a steel wall quickly bends and then retracts during a blast event. It typically happens so fast that it’s barely visible to the naked eye.
Dynamic load transfer is observed in many steel objects, like the springs in cars, flatbed trucks, and steel bridges. Flex allows a vehicle to take a greater load than it could without. And, if you’ve ever noticed the subtle movement in a bridge when a car passes over it, that is also flex.
When the steel in a blast resistant building flexes, it absorbs kinetic energy from the blast wave rather than reflecting it. (Although some of the energy is also reflected.) In a steel building, by limiting the amount of deformation in a design, dynamic load transfer is considered a protective feature and an advantage to a building’s safety. Other buildings that use rigid materials, like concrete, allow the blast wave to impact the walls, creating more reflective energy, focusing more stress on the building’s joints.
Cost of a blast test?
Some manufacturers invest a great deal of money in field testing their blast-resistant structures. You can estimate that a blast test of the scale referenced in this article could cost in the range of mid to high six figures. For this same reason, there are companies that do not perform blast tests, instead, relying on mathematical models, as previously mentioned.
When lives are at stake, we believe that the dollar amount of testing should not be a deterrent to protecting lives. As a leader in the industry, with a commitment to safety, we believe that a blast-resistant building should employ a tested and verified design, not just a design that is theoretically safe.
The RedGuard Blast Test
At RedGuard, we want our customers to know the lengths we go to determine that our spaces are safe and trusted. It starts with engineering and structural design, but it doesn’t end there. Putting our designs to the test is part of our process.
We call it being Tested for Life.
We’d never sell a building that we didn’t think passed that test. When all is said and done, the most important piece of our formula is that a building’s occupants go home safe at the end of the day.
Now that you have the facts about blast tests, and know that steel blast resistant buildings are the best choice for safety, even in high hazard areas, you might be wondering what it looks like in action.
You don’t have to take our word for it, though; you can watch the video or, download our blast test summary results!
Carreen Gibbons
Carreen Gibbons is the Communications Specialist at RedGuard. With a natural curiosity toward technical subjects and a love of learning new things, she writes content for the SiteBox Storage and RedGuard websites and spends her days learning new things about the industries that the companies serve.