Safety & Regulations | Best Practices | Design & Engineering
After the Sale: Managing a Blast-resistant Building Project
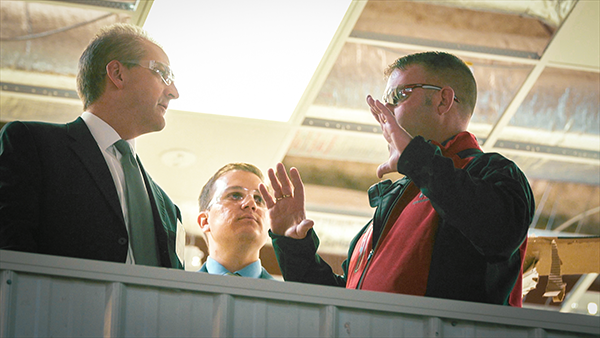

If you’ve purchased a blast-resistant building, or even if you’re still in the bid phase considering your options, you may be wondering what happens once you send in the purchase order. Once the deal is done, is it just a matter of waiting?
Not quite.
There are many of steps that happen between the time you send in the purchase order and the time your blast-resistant building is delivered. When you choose to work with an experienced company like RedGuard as your partner, you can be assured that the transition from sales to project management is a smooth one, with few surprises.
As an industry leader in designing and building blast-resistant modular buildings, RedGuard has seen thousands of projects through from start to finish. We’ve created a process that we know works. And, because we know blast-resistant buildings inside and out, we can make the process run smoothly, whether it’s your first project or your twenty-first.
The purpose of this article will be to review the steps that happen after the sale is made, during the project management and the manufacture of a blast-resistant building.
Because the process can vary depending on the vendor, we can’t guarantee that the process will be the same with every company. This article should give you a general idea of what happens during the manufacturing process and in the time leading up to it.
Moving into Project Management
Once a purchase order (PO) is received, the project is handed over to the project management group. At that time, a purchase order review begins to make sure that the company can/will accept the purchase order.
Not all POs are accepted immediately. Sometimes the blast-resistant building manufacturer requires changes in the contract language, or there could be details to be clarified before the PO is formally accepted.
Occasionally, some new specs may show up in this stage. For example, the purchasing agent may not have clarified the type of HVAC system required or whether the system should be redundant. Before the PO is accepted, the building vendor will send it back with language defining these types of details, and the customer will need to approve the additional details.
Depending on the complexity of the changes, and the responsiveness of those involved, getting the PO approved could take between a few days and a few weeks. The project manager will do what they can to ensure the process keeps moving until both parties sign-off on the PO.
The Kick-Off and Design Stage Meetings
Once the purchase order is formally accepted, the floor plan is emailed to the customer for review and an initial kick-off meeting is scheduled.
The kick-off meeting gives the salesperson the opportunity to introduce the customer to the project manager, and for the project manager to begin talking about expectations for the project. During the kick-off meeting, the customer has reviewed the floor plan in advance, allowing for more design conversations to begin. In this meeting, there will also be a detailed review of the architectural, mechanical, electrical, plumbing, structural, and blast components of the building. Additional meetings may be required for each of these components of the blast-resistant building.
Once the project is under the care of the project manager, the original salesperson will be relatively hands-off unless their assistance is needed. For example, their assistance may be required to discuss change orders or commercial changes, which occur when there are customer-driven changes that result in an increase or decrease to the contract price.
Depending on the customer’s preferences, calls will be set up weekly, or updates can be given periodically by email. The important part is to keep an open channel for communication flowing.
Blast-Resistant Building Timelines
There’s no real way to narrow down how long a blast-resistant building project will take since the timeline will vary based on factors like building size, design complexity, material availability, state-specific approval processes, and project backlog.
Project sizes can vary from simple single unit buildings, which may be ready in a matter of weeks, to large multi-section complexes which could take months, or the better part of a year. The best way to find out the timeline is to ask about the specific details for your project.
As a general rule, ask questions. How will the project be managed? What happens if we have change orders? Will this change affect my projected delivery date?
In most cases, project management begins when the order is accepted and ends when it leaves the vendor’s production facility. Once the blast-resistant building is installed, regular maintenance and any issues that come up are handled by a qualified service department.
Customer Approval and Finalizing Designs
Once the kick-off meeting has occurred, initial introductions have been made, and the customer signs off on the floor plan, then things begin to move forward. It’s important to have an approval process in mind on your end when approval is required at other stages. This will help the process run in a timely manner.
Other meetings that will need to occur and places where other approvals may come into play will be when discussing the architectural, mechanical, electrical, plumbing, structural, and blast components of the building. Each of these components will need to be reviewed and approved using detailed pdf files. These drawings will call out the placement and specifications for each of these elements, which were not detailed on the floor plan.
Third-Party Approval for Blast-Resistant Buildings
Each build-site is different as far as requirements for blast-resistant buildings. Some states have strict environmental guidelines (California comes to mind), some follow another set of standards, like OSHA or other federal, local, or regional guidelines.
Your blast-resistant building manufacturer will be responsible for ensuring that the building meets all requirements of the local authority having jurisdiction (LAHJ) and will set up any third-party reviews that need to happen.
These requirements could add things like fire sprinklers, devices to improve air quality or emissions, or any number of details meant to protect the occupants of the building. It is the responsibility of the vendor to know and expect these requirements.
Construction of the Blast-Resistant Building
Because they are modular in nature, the construction of blast-resistant buildings happens before they ever get to your site. This is one of the greatest benefits of modular construction.
In short, this means there’s much less of an impact on your site operations. There’s no period of downtime for the space the building will occupy. There’s no working around the mess of a construction site. There’s no re-routing of trucks.
During the construction phase, the customer will get updates as needed, including progress photos. There’s no way to nail down how long the construction of a blast-resistant building will take because each project is different. It’s all dependent on the construction queue of the vendor, the size of the building, and the complexity of design and elements.
A typical build, for example, a simple three-plex or smaller, may take 16-20 weeks from the time drawings are approved. Other complex projects will take more time. Your vendor should be able to talk in more detail about this, based on the specs of your individual project. There are occasionally ways to expedite builds, but it’s not a good practice to rely on that to happen.
The last thing to happen while the building is still at the vendor site is the factory acceptance test. The building is put together at the facility, just like it would be on the customer’s site. Some customers may choose to do a final onsite walk-through; others may give approval based on photos of the finalized building. This can typically be done in a day.
Transportation and Installation
Once the final walk-through has happened, there will be no time wasted before the build is on the road. If the building is a multi-plex, it could take several trucks to get it to its final destination.
Some companies have their own transportation fleet, while others rely on outside sources. And some will use a combination of their own trucks and third-party transportation sources.
Project Management Challenges
According to the project managers at RedGuard, working through the design process without delays is the biggest challenge in managing blast-resistant building projects.
Designing a building requires a lot of information and input from the customer. Sometimes there is information that is not available during the bid phase.
Awaiting Details
Examples of some information that may not be available before the PO is issued are things like the actual electrical load requirements for equipment that is supplied by the customer, the expected use for each room in the building, and final details like color or finish selections. Waiting on these things can slow down the initial design process.
Getting Everyone Involved
Another hold-up is that sometimes the person who’s been involved on the customer side, the purchasing agent, isn’t the end-user of the blast-resistant building. Once the end-users become involved, they may have valuable information or knowledge of the project that will require changes during the initial review. For this reason, it’s helpful when decision-makers and the building’s users are both involved during the bid process, so all details are resolved prior to project award.
Change Orders
Change orders are a fact of life in the management of blast-resistant building projects, so it’s not the worst-case scenario when they come up, but avoiding them will always save you time and money. Following the advice here, as well as keeping the lines of communication open, and the team informed, will serve you well.
Wrapping It Up
At RedGuard, we design and build blast-resistant buildings and have been doing it since 2005. All the related details are on our minds every day, for at least 40 hours a week, but we know that our customers have more to think about. That’s why our team of experts, in Sales, Estimating, Engineering, and Project Management, are ready and willing to answer your questions and consult on your project.
No matter how much experience you have with capital projects or turnarounds, let’s start talking about your goals and see if it makes sense to put a RedGuard blast-resistant modular building on your worksite.
No two hazardous worksites are alike, so no two blast-resistant projects are alike. Our expert team can help you start planning your project to save you time, money, and, most importantly, lives.
Carreen Gibbons
Carreen Gibbons is the Communications Specialist at RedGuard. With a natural curiosity toward technical subjects and a love of learning new things, she writes content for the SiteBox Storage and RedGuard websites and spends her days learning new things about the industries that the companies serve.