Best Practices | Safety and Regulations | Hazard Protection Protocols | OSHA PHA | Site Inspection
3 Signs You Need to Implement Better Hazard Protection
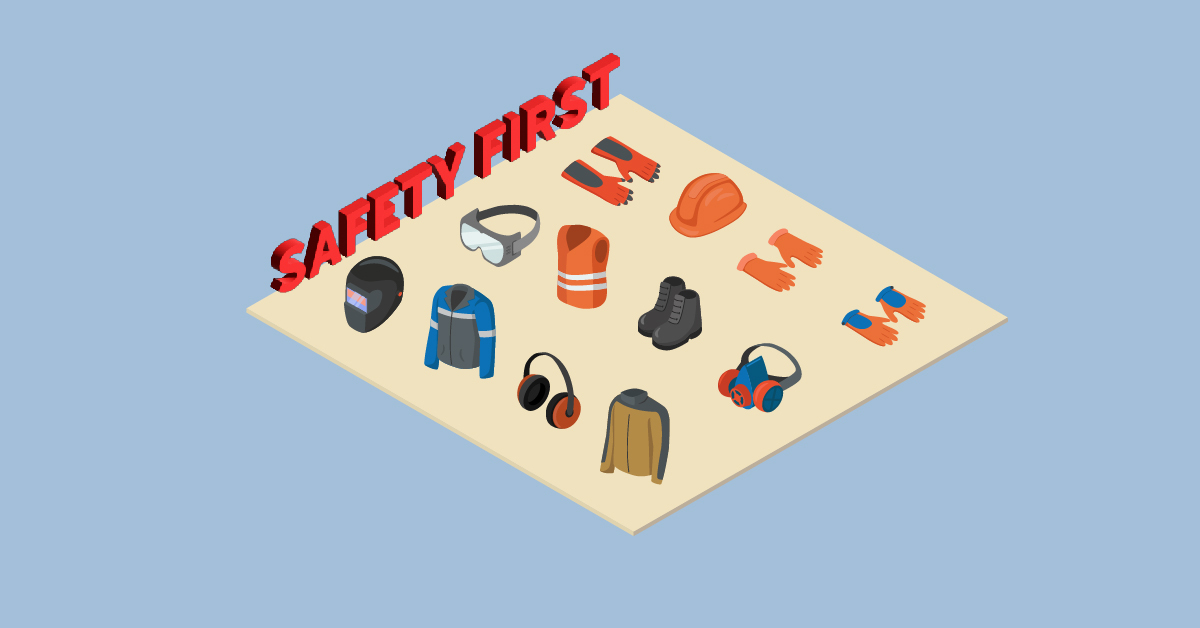

Protecting workers from on-site hazards is a complex task. However, soliciting hazard protection analyses and addressing as many risks as possible can protect workers, prevent fines, and improve a company’s reputation.
Below, we will examine the importance of implementing hazard protections on work sites and identify three signs that your company needs to update or improve its hazard protection protocols.Sign #1: You Failed an Audit or Inspection
OSHA's Process Hazard Analysis (PHA) applies to facilities that deal with highly hazardous chemicals and requires companies to take specific precautions "for preventing or minimizing the consequences of catastrophic releases of toxic, reactive, flammable, or explosive chemicals [which] may result in toxic, fire or explosion hazards."
One of these precautions is a facility siting study designed to assess the possible results of a fire, explosion, or chemical release by looking at equipment, instrumentation, utilities, human actions, and external factors. Siting studies are also initiated during new construction to help identify any safety concerns related to new buildings or equipment.
These safety precautions are mandatory, and companies that skip or fail them are subject to prohibitive fines from OSHA. Of course, using the proper risk assessment will help you avoid the most significant risk - seeing a worker harmed because of an avoidable site issue.
Preparing for an Inspection
There are a few things to know before getting a facility siting study. First, you can choose a vendor to perform the study, and they will arrange for a Process Safety Expert or Engineer and a Structural Expert or Engineer to tour your site. A technician may also accompany them to help measure and document buildings. Choosing a vendor with a good reputation and certified expertise is best since the purpose is not "box-checking" but to assess your operations thoroughly. Their goal is to gauge the type of outcomes a company can reasonably expect in the event of a blast, fire, or chemical leak - that way, you can make a plan to implement appropriate hazard protections.
What Happens During a Site Inspection?
Site inspectors will get in touch ahead of time and request instrument diagrams, site plans, and written emergency procedures. They will also communicate the information they intend to gather and the instruments they need to gauge safety. To be proactive, you should inform the inspector of PPE needs. Here's a checklist of other ways to prepare for the site study.
During their site walk, inspectors will ensure that site activities are similar to what's stated in your safety protocols and other records. The inspectors will take photographs, make notes, ask questions, and access indoor and outdoor areas on the site.
Vetting companies to identify the most reputable site safety inspectors is the key to thoroughly assessing all risks and remedies.
Avoid Failing an Inspection
No company is perfect, so there will always be room for improvement. It's essential to expect feedback and take it seriously to avoid accidents and manage liability.
The facility siting study is critical to implementing better hazard protection for workers. It's also a document that goes on the record. So, if a worker is harmed on your site and you were warned it could happen during a site study, a reluctance to fix it right away can lead to financial and reputational damage. If OSHA audits your facility, a thorough siting study can show inspectors that you've made efforts to maintain a safe environment. Failing an OSHA inspection can result in fines up to $70,000 per violation.
Sign #2: Your Team Doesn’t Know What to Do In Emergency Situations
You may have a relatively safe worksite with excellent blast resistant buildings and other safety mechanisms in place. However, these tools will not be fully beneficial if your workers aren't properly trained.
The goal of any company when it comes to hazard protections is to go beyond mere compliance and create a culture of safety that focuses on preventative education rather than policing and after-the-fact punishment.
Hazard Protection Training
No one enjoys endless safety orientations and training, especially if the training is presented in an unrealistic or cumbersome way. Also, it's easy for workers to skip donning layers of PPE or adhere to laborious safety checklists whenever they need to perform a task. Therefore, reinforcing PPE practices through meaningful examples is crucial for getting workers to take safety seriously.
Safety training needs to address real-world examples and consequences. This may require:
- Investing more money in better training and safety updates
- Providing incentives for attending safety training and maintaining good records regarding hazard protections
- Updating training for long-time employees
- Providing new protocols when new equipment is installed
- Ensuring easy access to safety information outside of training sessions
It's also critical to understand the role of complacency and fatigue in abiding by safety protocols and emergency action plans.
Suppose workers are overextended, put under time pressure, or operate in an atmosphere of punishment, not trust. In that case, companies are much more likely to see burnout that can result in accidents or find that some safety mishaps were never recorded.
Reacting to Hazards, Emergencies, and Near-Misses
Testing protocols that allow employees to physically act out an emergency plan can ensure there's no panic during a real emergency. These safety drills can be crucial in alleviating anxiety and addressing uncertainties about where to go, what to do, and who’s leading the way when hazards turn into emergencies.
By creating a culture of safety and replacing the fear of punishment with rewards for reporting hazards, companies can also encourage employees and managers to report near-misses.
Most incident reporting is reactive, occurring after an incident has transpired. Recording near misses is a proactive hazard protection strategy in which companies record an "unplanned event that did not result in injury, illness or damage – but had the potential to do so." Even though they may not cause harm in the moment, near-misses can provide companies with data to help prevent future incidents.
Sign #3: Incidents or Close Calls Have Occurred
Each year in the U.S., around 3 billion "close calls" or "near misses" occur on job sites. For every 300 of these, 29 result in minor injuries, and one in injuries severe enough to keep a person out of work.
In a 2010 speech to the National Petrochemical and Refiners Association, OSHA's Deputy Assistant Secretary Jordan Barab noted that most safety records don't tell the whole story and that "having good numbers on your OSHA 300 logs doesn't correlate with having an effective process safety program."
Often, companies don't find out where their weaknesses lie until a disaster happens. Barab warned refineries not to "let those numbers lull you into a false sense of security." Disasters strike facilities with stellar safety records, and Barab got right to the point, warning companies that "giving awards to your members based solely on a lack of slips, trips, and falls doesn't make you look like a serious organization. If you want to be taken seriously, you need to act like an organization that recognizes there are serious problems and an organization that is seriously addressing those problems."
What Happens After a Near Miss?
Near misses or minor incidents on a worksite can also have a psychological effect on workers. That's why addressing these as soon as possible is critical in demonstrating support for improving safety conditions. Workers need to know you value their safety so that near misses never become actual accidents.
Ideally, a near miss will be a wake-up call. A company's reporting system will alert management to the problems and provide an opportunity to implement new hazard protection protocols.
OSHA recommends involving workers in identifying safety measures to prevent future incidents. This involvement gives them ownership of the safety protocols they're required to follow and ensures maximum compliance.
Collecting ideas about hazard control and doing so during working hours shows employees that safety is part of the job.
Some incidents that involve technical equipment may require third-party intervention by safety professionals or engineers. Even then, it's crucial to involve employees in these assessments.
Securing Your Site with a Blast Resistant Building
One of the best ways to help avoid worksite incidents on sites prone to fires and blasts is to install blast resistant buildings to contain sensitive equipment and give workers a safe workplace.
Once you've conducted a site study and defined your needs, RedGuard can help you identify or customize a blast resistant building. We have various blast-resistant building options, including leased temporary modular buildings for sites that don't require permanent solutions. RedGuard's blast resistant buildings are also available as turnkey pre-engineered buildings.
All RedGuard buildings are constructed off-site to minimize worksite disruption and are specifically engineered to match your needs.
How to Improve Your Hazard Protection Protocols
According to OSHA, developing and updating your hazard protection plan involves prioritizing the most serious hazards and implementing interim protocols if developing a comprehensive long-term solution requires more time. In addition, companies should track their progress toward their ultimate goals and check in annually to verify that the controls are still adequate.
Select workers to help identify and implement safety controls so it's clear who to consult regarding new protocols and update timelines. Then, establish metrics for tracking the efficacy of new safety controls.
RedGuard’s Dedication to Safety
Implementing hazard controls on work sites is a necessity but not a guarantee of complete safety. Companies need to conduct siting studies using thorough, reputable companies with engineering expertise. Most importantly, they need to use these studies to address any safety inadequacies as soon as possible.
At RedGuard, we also use OSHA's TRIR, or Total Recordable Incident Rate, to help gauge worksite safety. The TRIR formula is:
The total number of recordable injuries or illnesses X 200,000 divided by the total hours worked during the year.
The number 200,000 is derived from OSHA's estimate of 100 employees working 40 hours a week for 50 weeks. However, it’s important to note that this does tend to penalize smaller companies, and is why it is considered a "lagging indicator." Regardless, it's essential to know your rating because higher numbers can trigger OSHA inspections. While the TRIR isn't a perfect metric, it is the OSHA standard, so it's essential that your safety studies provide you with this number.
At RedGuard, we keep our TRIR number under the lowest standard rating of 1 (meaning one injury per 100 workers - the industry average). RedGuard strives for a TRIR of 0.9 to quantify our safety performance, and because some customers hold us to a TRIR of less than 1.5 or even less than 1. This indicator is another way we help companies keep their workers safe and provide optimal hazard protection for your site and crew.
To learn more about our commitment to hazard protection, contact RedGuard today.
Bryan Bulling
Bryan Bulling is a Regional Area Manager for RedGuard, serving the Northeastern United States. He's an expert in the areas of hazard consultations and blast-resistant solutions. He has more than thirty years of experience in a range of industries, some of those include construction, industrial/commercial architecture, oil and gas refining, and project planning.