Articles | Safety & Regulations
How to Create Safety Culture in a Refinery
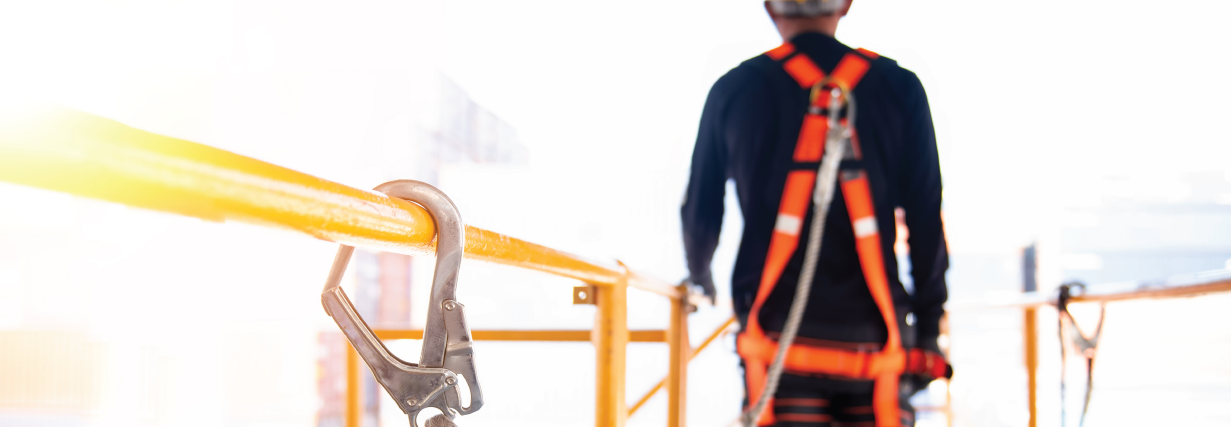

At RedGuard, we realized from the beginning that having a culture centered around safety just made sense. We create a product designed to keep people safe, to ensure that at the end of the day, someone working in one of our buildings is going home to their family, even if the unthinkable happens.
It only made sense that we would follow the highest guidelines of safety in our own practices. We believe that our people are our best asset, so we do all we can to protect them. That starts with behavior. But how do you change someone’s behavior?
You Can’t Tell Me What to Do!
Few folks want to be told what to do or how to act even when it’s in their best interest. This principle has shown itself boldly with teen vaping. Wagging a finger to make a point of how harmful – if not deadly – this habit is, has far less effect than showing teens how to be empowered. Empowerment instills a strong sense of self-worth and confidence. It allows people to make educated choices. So it is with safety too.
What’s the Difference Between Safety Compliance and Safety Culture?
Having a culture that permits employees to be actively involved with setting, monitoring, and enforcing safety goes above and beyond mandated enforcement. OSHA, or the Occupational Safety and Health Administration, sets and regulates safety standards. Compliance is the act of abiding by the rules.
Enforcement and training on subjects that are already in practice and monitored do little to move the needle on safety measurements.
For example, mandatory refresher classes on PPE, though a great reminder, often are seen by employees as simply “checking the box.” It certainly updates the records for the safety manager, but it leaves few lasting impressions on the trainees, especially after continuous years of service and multiple mandatory training sessions.
The PPE procedures haven’t changed much in the last several years. It doesn’t take a rocket scientist to do the math. If five mandatory training sessions were completed each year for a refinery of 100 employees, the total working hours spent on non-effective, but compulsory training equates to 500 hours. Plus, factor in time spent on the preparation, presentation, and paperwork time of the instructor.
By comparison, allow the collective values and actions of workers – the culture – to drive the expectation that provides buy-in. Lifestyle decisions are the way the group chooses to thrive. A culture of safety demonstrates shared values of deliberate awareness, workplace/machinery risk reduction, and behavioral norms that reduce hazards.
A culture where employees feel free, without retribution, to call-out a fellow employee’s oversight on a safety miscue can be more impactful and timelier. When a person’s respiratory gear shows wear or lack of protection and a colleague takes notice and comments, both employees are much safer.
OSHA is strict, but it serves a purpose. If facility siting studies were not mandated in OSHA’s Process Hazards Analysis (PHA) section of the National Emphasis Program (NEP), the general working population of refineries may not even be aware of the availability of such lifesaving measures. Conversely, OSHA cannot write enough regulations to stave off human error; co-workers will always be more effective in this area.
The Difference Between Policing Safety and Educating
There is a marked distinction between educating and policing. When employees move to a heightened awareness of refinery safety and understand how things like complacency and fatigue contribute to unsafe working conditions, it is so much more effective than just policing them and calling them down, or worse – putting them on a list or disciplining. Policing rarely has a positive effect. It can create an atmosphere of fear and distrust. Employees don’t want to rat out co-workers.
The adage is, “If you want to learn, teach.” Find your champions. Find teams of people that will champion and teach. Find those who will model and mentor. These people are your “safety advocate team” and their genuine concern about safety will set a positive example. Support them in their endeavors to help build a safety culture because they ‘get it’ and because they care. Making sure they have top-down approval for new ideas, or even a small budget to spend on incentives or materials to teach others goes a long way.
In the short term, watch for behaviors to change and keep giving positive reinforcements for even small changes. After a year or two, compare the safety ratings and recordables of your company against those same figures of the previous years.
Creating a Culture of Genuine Care
Why would employees want the responsibility to be their brothers’ keepers? Because he hopes that someone is looking out for him as well. So much of our lives are spent with our co-workers.
Companies that value investments of time and energy to select employees that fit into a culture of genuine care for fellow employees will, in the end, spend less time and energy generating compliance.
Collaborate, teach and live out principles. It’s much more cost-effective than dealing with a poor safety record. In the end, creating a culture of genuine care creates a culture of safety.
Building a culture within an organization is a deliberate and worthwhile endeavor. Leadership has a lot of options of study. Best-selling author Jim Collins’ books have been a proven source of research that can be a valuable resource.
For instance, when employees begin to understand the ‘window and mirror’ approach of Jim Collins’ teaching, culture takes hold.
This principle puts forth that when one looks in the mirror, he sees himself and identifies his shortcomings, taking ownership of negative outcomes, including safety infractions, that he could have prevented. This could include realizing that you’ve developed lazy habits when it comes to wearing the correct protective gear, or that you don’t always use a safety harness when working at height. The individual who realizes this and changes the behavior builds trust with the team. This person owns up to his shortcomings.
When looking out the window, one sees others and recognizes their contributions. Appreciation of good performance and giving credit where credit is due builds successful teams. This person recognizes that success is never achieved alone. So does a TRIR or EMR rating – it’s a collective rating of the group performance.
Effects of Building a Safety Culture
Accidents rarely impact only one person. If a worker bypasses lock-out and tag-out (LOTO) practices, the effects are far-reaching and can extend beyond even the refinery boundaries.
Safe work practices benefit families. It protects their source of income by keeping the refinery operable and profitable. It protects the paychecks of the families. It protects the economy of the families and region reliant on the refinery as part of the job market. It keeps the product flowing to the consumers.
Building Your Own Safety Culture
If your company is simply enforcing safety, perhaps you are missing the point as well as falling short of an exponential reduction in ratings. Start working in your company to build a culture of genuine care and concern among employees so that they care about one another - that even extends to their families. Look at your hiring practices, examine the hearts of management, offer benefits that propagate the value of the employees, reward workers that demonstrate true concern for colleagues and safety.
The truth is, the pendulum swings, and never will regulation or culture stand alone. At times, it can feel like an organization is more on one side than the other. It takes both – in equal measures – to have a balanced approach.
The hope is that you find the perfect balance to achieve a great safety culture in your workplace. Being able to utilize the ‘Genius of AND’ (another Jim Collins principle for great companies) to embrace regulation and compliance AND create a culture of employees that care about one another and the importance of everyone going home safely to their families.
RedGuard has found a way to bring safety into our everyday lives as we go about designing and building blast-resistant modular buildings. We create the buildings that keep people safe even in the most hazardous areas of a refinery. In the end, we care about people.
Lorna Geist
Lorna has been with RedGuard since 2012 and is a sales specialist. Her specialty is generating quotes for all the creative ways our customers use LeaseFleet buildings. She is also a member of the LANGE culture committee, which focuses on keeping employees from RedGuard and all LANGE companies focused on our core values.