Best Practices | Safety and Regulations | Hazard Protection Protocols | OSHA PHA | Site Inspection
5 Steps to Ensure Your Company is Protected from Hazards
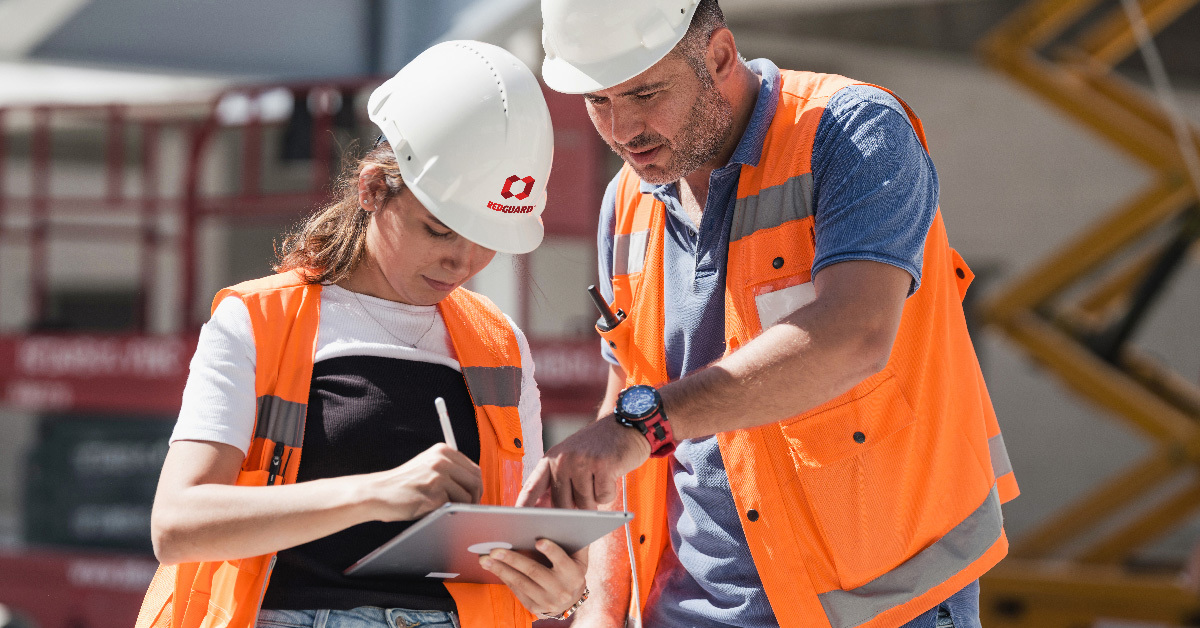

Protecting employees from workplace hazards requires formal control mechanisms and detailed planning. The most effective way to accomplish this is to use a "hierarchy of controls," a step-by-step process that allows safety managers to choose all the relevant tools needed to eliminate hazards or protect employees from dangers.
While options at the bottom of the hierarchy are less effective, if the other tasks prove impossible, facilities should attempt to employ administrative controls to change how people work around hazards and provide PPE as a last line of defense.The hierarchy of controls is relevant to all manufacturing facilities. However, it is crucial for those industries with high risks for workers, such as oil and gas, petrochemical, nuclear power, electronics, and metals.
Below, we'll look at the five steps you can take to eliminate, substitute, or protect employees from hazards to ensure your facility is as safe as possible.
Step 1: Stay Up-to-Date with Regulations
Staying on top of regulations is more than mere paperwork. OSHA's Process Hazard Analysis (PHA) requires companies to take precautions "for preventing or minimizing the consequences of catastrophic releases of toxic, reactive, flammable, or explosive chemicals [which] may result in toxic, fire or explosion hazards."
For example, manufacturing plants that process hazardous materials must perform a facility siting study to assess the consequences of a fire or explosion. This requires examining equipment, utilities, safety plans, and any external factors that could lead to fires and blasts.
A siting study must also be performed when new buildings or equipment are added to a job site. Failure to perform a facility siting study can result in hefty fines from OSHA and, more importantly, accidents on a job site. Since companies can choose their own site inspectors, it's crucial to choose a company that does a thorough job and suggests remediation plans.
Step 2: Develop a Hazard Control Plan
Even the most compliant worksites are subject to external factors that can cause fires and explosions, such as lightning strikes. That's why all worksites need a hazard protection plan. According to OSHA, these plans are designed to identify hazards, implement safety protocols, assess the protocols regularly, and ensure employees are trained to act according to the formal plan.
Hazard control programs should be updated periodically, as well as any time new equipment and processes are integrated into a work site. Without training employees to act, having a written action plan is of very little use. It's also crucial to develop metrics to help judge whether hazard control protocols are effective.
One of the best ways to help workers avoid injury during a hazardous episode is by installing blast resistant buildings on worksites. These can be used to serve as shelter to workers. For example, RedGuard's blast resistant buildings can protect workers from heat, fire, shrapnel, and other dangers.
RedGuard's buildings are turnkey building solutions that are constructed off-site to minimize workplace disruptions and risks. They're also customizable, so our staff can help you identify a range of options to help you meet safety requirements on site. Even better, we'll help you arrange a third-party inspection for maximum protection.
Step 3: Conduct Inspections
Conducting inspections must be completed by a third party to ensure facilities can get an objective assessment of any potential shortcomings.
The goal of these inspections is not just to ensure tools are in working order but to give managers a sense of what they can expect if accidents do occur. Since not all incidents can be avoided, it's crucial to go beyond prevention and make a plan for the worst-case scenario. Managers can then prioritize fixes and better safety measures, including updated hazard protection training and emergency action plans.
RedGuard's buildings are constructed using a design that was successfully blast tested by third-party engineers to ensure they can withstand the pressure and keep people safe. When lives are on the line, companies need proof that their safety investments will pay off. That's one of the reasons RedGuard uses third-party engineers to test our units with maximum objectivity.
Not only will RedGuard perform a safety assessment on your site to analyze potential hazards related to explosions, fires, and toxins, but our team can also provide overpressure maps to calculate damage from potential explosions. RedGuard's buildings have been blast-tested, and we're one of the only companies that post the results of blast tests online.
Step 4: Practice Emergency Protocol
You can have a job site that meets all safety requirements, but if your team doesn't know how to execute an emergency protocol, nobody is protected. Even in the case of a blast resistant building, employees have to recognize when to take shelter.
If your team doesn't know what to do in the event of an explosion, it's critical to implement consistent training and offer refresher courses annually (as well as any time there is new equipment on site). Even in the event that an act of nature sparks a blast, workers have to know what's happening, where their team members are, and how to get to safety. A blast resistant building can't protect workers who don't know when to use it, and that often requires staging drills so that everyone has acted out the safety protocol at least once.
Step 5: Conduct Routine Maintenance
All safety equipment requires routine maintenance. For example, on blast resistant buildings, heavy use of doors and windows necessitates building upkeep, and HVAC tools must be kept in good shape to ensure the building provides a safe haven for employees. When a blast resistant building is installed, companies need to ensure they get guidance on getting preventative maintenance, renovations, and upgrades.
RedGuard services its blast resistant buildings, so we're familiar with the kind of care they tend to need. The most common service calls involve HVAC/AC performance, door and door handle maintenance, and issues with ceiling or floor tiles. Our team can even help inspect and repair blast resistant buildings from other companies.
RedGuard Blast Resistant Buildings
Whether you're looking to buy a modular blast resistant building, schedule an audit, maintain, or assess your safety guidelines, RedGuard can help. We are proud to offer:
- Facility Siting Studies
- Process Hazard Analyses
- Process Safety Management (PSM) Audits to evaluate process design, technology, operational and maintenance activities, emergency plans, and training programs.
- Quantitative Risk Assessment (QRA) to help you quantify your highest priority risks
Not only do we create customized and blast-tested blast resistant buildings, but we're also committed to improving safety in every way on your job site.
Learn more about our engineering services for hazardous worksites or schedule a consultation with one of our experts.
RedGuard Sales & Marketing
The RedGuard sales and marketing team curates and writes on a variety of topics regarding blast-resistance and modular buildings. To inquire about any of the topics you read about on our blog, connect with us.