Petrochemical Industry | Petrochemical Industry Explosions
What Causes Oil and Gas Refinery Explosions?
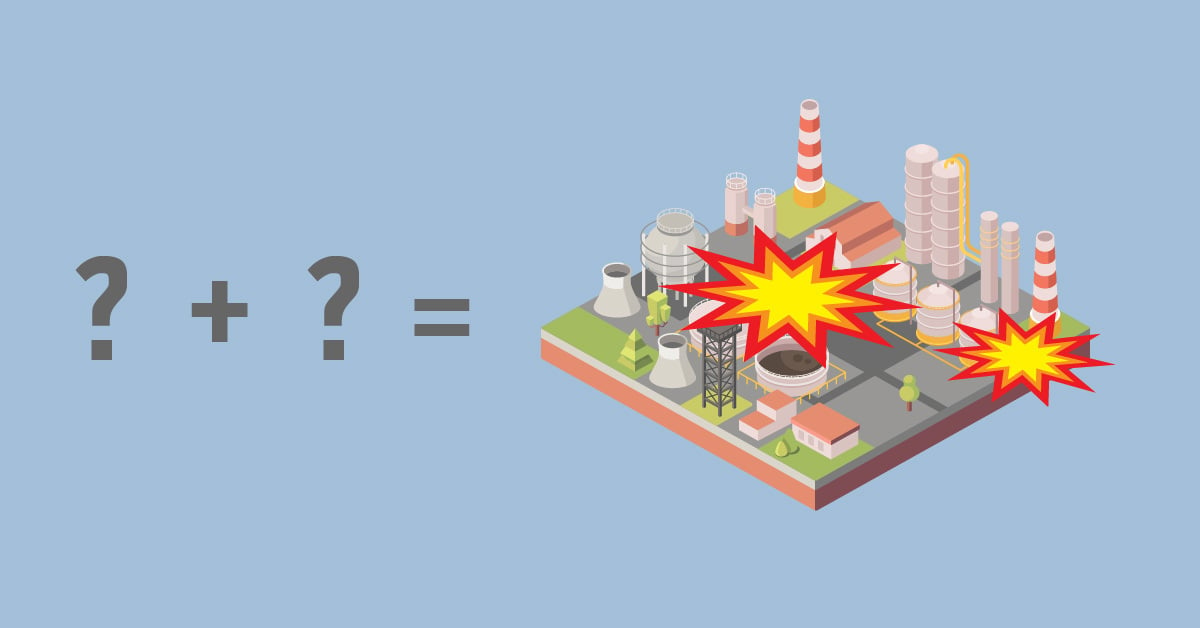

Explosions in the oil and gas industry are rare, but when they do occur, they can have devastating effects on workers and even nearby residents. These blasts can cause burns and shockwave injuries that cause internal damage, head injuries, and nerve damage. Also, flying debris following an explosion can cause severe lacerations and blunt-force trauma.
Most workplace incidents at oil and gas refineries are caused by transportation and equipment accidents, followed by fires and explosions.
The vast majority of blasts on oil and gas worksites are preventable, particularly when facilities managers uphold OSHA safety regulations. Below, we'll examine some of the causes and how to avoid them so you can keep workers safe and avoid damage to people and property caused by blasts.
Defective Equipment
Equipment can malfunction due to defects or negligence. Incidents resulting from defects can be hard to prevent since they often start outside the refinery, at the equipment’s manufacturing facility. Shoddy construction and poor instructions from the manufacturer can put workers at risk even when operating machinery according to guidelines. But faulty design can also play a role if the equipment is used in a way other than it was intended, repaired with non-standard parts, or put under more stress than planned. Luckily, process safety managers can prevent these issues.
Equipment accidents should be taken seriously, since they are the second most common cause of injury and death at oil and gas refineries. Safety managers can help prevent catastrophes by ensuring equipment is used correctly and is adequately inspected and maintained. And perhaps most importantly, training employees to use machinery safely and recognize the signs of potential malfunctions early, can help keep everyone safe.
Even under the best circumstances, extracting gas and oil is dangerous. That's why OSHA mandates that refineries study worksite hazards, warn employees about them, provide workers with personal protective equipment (PPE), and establish a training and response plan.
'Dirty' Chemicals
Refinery sites, by nature, contain flammable gasses and vapors from wells, vehicles, and equipment, as well as volatile chemicals. Because the goal of refineries is not only to extract oil and gas but also to purify them, chemicals are used to help "clean up" impurities. In cases where trace amounts of the chemicals remain, leak out of storage, or are exposed to moisture or temperature variations, they can contribute to the fires that cause explosions and the injuries and inhalations that result.
By maintaining all equipment, training employees in safety precautions, providing ventilation, and using blast resistant buildings on refinery worksites, safety managers can help avoid accidents or at least mitigate the damage they cause.
Well Blowouts
An oil well blowout refers to the uncontrolled release of crude oil. Refineries take many precautions and have pressure release systems to ensure this is an infrequent occasion. Still, they happen, and when they do, they can release methane, benzene, and other toxic air pollutants into the atmosphere that affect on-site workers and residents in the area. These pollutants can cause issues like headaches, long-term respiratory issues, or even cancer.
Oil well safety and maintenance are vital to reducing the risk of blowouts. Mechanical barriers and close monitoring for signs of a blowout are also necessary to keep refinery worksites safe.
Unseen Corrosion
Safety managers and other employees are responsible for reducing the risks of corrosion and other signs of metal fatigue in refinery equipment and machinery. Metals with sulfide impurities, poorly applied coatings, and other faults must be adequately and proactively monitored.
Predicting corrosion rates and enhancing metals to prevent corrosion is part of every refinery’s safety program. Corrosion is a challenge in nearly every industry that uses heavy equipment and metal construction materials. Prevention with tools such as corrosion inhibitors is always preferable to mitigating damage since it can be widespread, cause extreme harm, and cost companies billions of dollars.
Human Error
Human error is at the root of most oil and gas refinery explosions. These errors can occur at any point and cover a wide range of deficiencies.
Deficient Safety Protocol and Unsafe Procedures
Oil and gas refineries require a safety manager to oversee a worker protection and equipment maintenance program. However, it is important to keep in mind that not all safety programs are created equal, and good ones require constant oversight and a commitment to safety from every worker to succeed.
Lack of Proper Training
Even with the best safety program available, a refinery can still experience an explosion if employees aren't trained to use equipment properly. Training is also critical for employees to keep a clear head and make good decisions when an accident occurs, even if it wasn’t anyone’s fault.
Improper Maintenance
Taking shortcuts with maintenance is an OSHA fineable offense and highly unethical. Even when executives and safety managers provide the necessary resources, they must also monitor equipment for any unexpected maintenance needs, trust workers to recognize damage, bring it to managers’ attention and rely on technicians to repair equipment correctly.
Cigarettes Starting Fires
It's common sense that you shouldn’t light a cigarette anywhere near a refinery, but it has occurred. In fact, cigarettes have caused serious industrial accidents in the past.
"No smoking" signs are too ubiquitous to stand out to most people, so educating employees about the risks of smoking on or near a refinery must be taken seriously as a part of a refinery’s safety program.
Safety Training and Explosion Mitigation
As of July 2022, the Bureau of Labor Statistics (BLS) reported that the oil and gas industry employs more than 590,000 people in the U.S. The industry typically sees over 100 workplace fatalities each year. In 2020, this number decreased to 78 (perhaps due to the pandemic). The number of workplace incidents in the refining industry has been steadily declining in recent years, and according to the BLS, there were only 1.2 injuries and illnesses per 100 workers.
In most cases, human error or negligence plays some role in explosions at oil and gas refineries, whether due to poor training or irresponsible behavior. However, the good news is that human errors can be mitigated with proper management, regular trainings, and up-to-date protocols.
Protecting the Petrochemical Industry with Blast Resistant Buildings
Not all blast resistant buildings are created equal, and chemical facilities have unique needs. In order to protect your team, you must utilize blast resistant buildings.
It's critical to choose a building based on its ability to withstand a blast and any resulting flash fires. Steel structures are the best choice since they're designed to withstand the shockwave of an explosion. Steel has the ductility and tensile strength ideal for blast resistance and can withstand the pressure of a blast of up to 9.9 psi. The ability to install a blast resistant building on a job site with minimal disruption is also crucial.
RedGuard's customizable, steel blast resistant buildings are ideal for petrochemical facilities because they are built off-site and come with the peace of mind provided by blast testing. RedGuard's buildings have also been blast-tested by third-party engineers to ensure they can withstand the pressure and keep people safe. When lives are on the line, companies need proof that their safety investments will pay off. That's one of the reasons RedGuard uses third-party engineers to test our designs objectively.
If you’re interested in learning more about RedGuard’s steel blast-resistant buildings and installation process, get in touch with our team today.
RedGuard Sales & Marketing
The RedGuard sales and marketing team curates and writes on a variety of topics regarding blast-resistance and modular buildings. To inquire about any of the topics you read about on our blog, connect with us.