Design & Engineering | Safety and Regulations
The Problems of Installing Concrete Blast Resistant Buildings
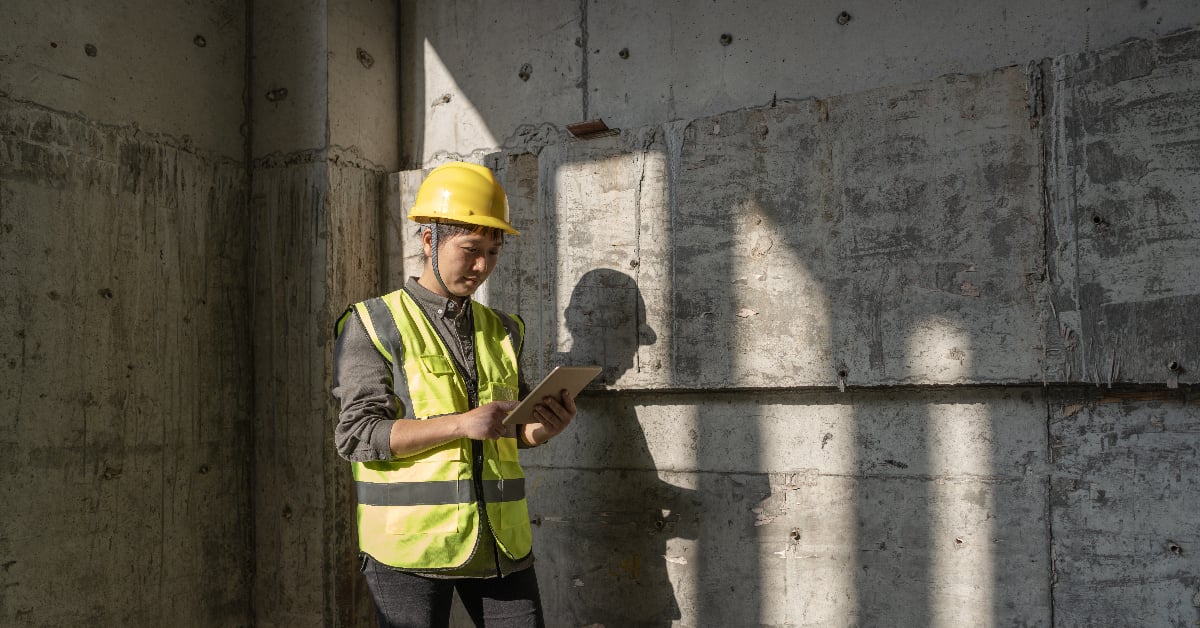

Blast-resistant modular buildings are designed to help prevent devastating damage to people and property in the wake of an explosion. Ideally, these buildings are strong enough to withstand ground motion, surface bursts, and compression from shock waves without collapsing or creating any flying debris that could harm bystanders.
Since WWII, we've known that buildings made of steel hold up better than materials such as concrete and brick. And, while some blast-resistant buildings are made of concrete, these buildings can pose challenges on job sites, such as laborious installation processes. That's why many companies in blast-prone industries choose blast-resistant buildings made of steel.
Below are just some of the problems with concrete, showing that it fails to provide the appropriate protection and convenience needed.
Problem 1: Concrete is Heavy
When thinking about materials that hold up to explosions, it's logical to believe that thick, heavy buildings are ideal. But in reality, materials with high ductility stand up better to blasts without producing any harmful debris. In this case, steel's tensile strength (its ability to bend, but not break) makes it a superior material for blast-resistant buildings.
The weight of concrete can make it a challenging material for job sites. Concrete structures are too heavy to be built off-site, so work has to wait while they are installed and inspected.
If time is a factor on a job site, it's rare for a work crew to be able to wait around while a concrete building is constructed. And industry best practices should prevent companies from starting work without this kind of protection for employees.
Heavy concrete structures also put excess pressure on foundations and aren't moveable, ductile, or recyclable like steel. On the other hand, steel can be light enough that smaller modules don't even require a foundation, making it easier to build the structure off-site.
Problem 2: Concrete is Expensive
While worker safety is paramount, the cost of blast-resistant buildings is an important consideration. When it comes to blast-resistant buildings, cost means more than just the price paid for the building itself–it includes labor and installation costs, time and money lost during the installation, and the cost of maintenance.
Steel costs less than concrete, partly because there is a market for recycled steel. It's also lightweight, making its transport cheaper and faster. On the other hand, concrete is much heavier and more expensive to transport, and it typically requires steel rebar as a reinforcement, which drives up construction costs.
Steel buildings have lower labor costs, especially if a site can use a prefabricated model. In addition, these buildings can be constructed off-site and installed quickly, exposing fewer skilled workers to the inherent dangers of the hazard area.
Overall, research has found that steel in construction results in a 5 – 7% decrease in construction expenses, based on a national average, making steel the more affordable blast-resistant building material.
Why Blast Resistant Buildings Should Be Constructed Off-Site
While having a blast-resistant structure built on-site may sound convenient, this doesn’t result in better or cheaper buildings. Prefabricated and custom buildings are easier to construct off-site (as long as the materials are light and easy to ship), offering other benefits.
Minimize Site Disruption
Working with the professionals at RedGuard starts with choosing a design. Then, while the building is fabricated and prepared for shipment, on-site preparation can occur simultaneously.
However, this work is not nearly as labor-intensive as pouring or assembling a concrete structure on a job site. That means ordering a steel blast-resistant building will minimize the disruptions to workers, so there's little downtime.
Protect Workers
Constructing a blast-resistant building on-site in a hazardous area would expose construction workers to danger, particularly if the building will be the only means of protection in the hazardous area. Additionally, codes and regulations designed to protect worker welfare create even more challenges for the construction of concrete buildings.
Off-site production means fewer people are exposed to hazards. By using off-site building and modular construction, you can keep workers safe while they build a blast-resistant structure.
Limit Liability
When a building is designed and fabricated off-site, it's easier to plan ahead to meet local and state regulations. Because employers are liable for employee injuries, ensuring that the final plans for a building meet the appropriate codes in advance can provide peace of mind to everyone and help employers avoid fines and lawsuits.
RedGuard's Installation Process
Choosing a trusted blast-resistant building vendor, such as RedGuard, allows companies maximum control over every step of the building and installation operations. Customers can expect to go through the following steps with RedGuard staff when they decide to order a blast-resistant building:
Consultation
To understand customer needs, RedGuard will ask about the building's purpose, whether it will be temporary or permanent, the site hazards in play, on-site accessibility and restrictions during installation, any utility needs (such as electricity), and the intended timeframe for the project.
Design
The next step is for RedGuard to use this information and expert knowledge of regulations to design the building or recommend a specific prefabricated model. Customized units take longer but can often better meet specific needs.
Build
A project manager from RedGuard keeps the client informed of the project’s progress. After completion of the build, the units are temporarily assembled so that the customer can do a physical or virtual walkthrough before it is shipped to their worksite.
After approval, the project is disassembled and shipped quickly.
Installation
The delivery and installation of anything can be disruptive to a worksite. Blast-resistant buildings are no different. That’s why it’s a good idea to minimize disruption. It may require several trucks and large equipment, such as cranes, to unload the sections of the project.
Assembly takes space and time, as skilled professionals hook up electricity, plumbing, communications and join and connect the sections of each building, as necessary. However, the inconvenience is minimal compared to what's required when building a concrete unit on-site.
Operation
RedGuard maintains close contact to ensure safety and satisfaction as the customer begins using the building. In addition, our expert team is always available to answer any questions during the entire process.
When choosing a blast-resistant building for a job site, steel wins out when it comes to safety, cost, effectiveness, and convenience. While steel-reinforced concrete has its benefits, the structure and labor costs, combined with the inconvenience of installation, may not be worth the investment in the long term.
Click below to read our Steel vs Concrete Head-to-Head Comparison.
RedGuard Sales & Marketing
The RedGuard sales and marketing team curates and writes on a variety of topics regarding blast-resistance and modular buildings. To inquire about any of the topics you read about on our blog, connect with us.