Best Practices | Design & Engineering | Custom Buildings | Blast Resistant Buildings | Hazard Protection
Precision Safety or Multi-Hazard? The Right Approach for Blast-Resistant Buildings
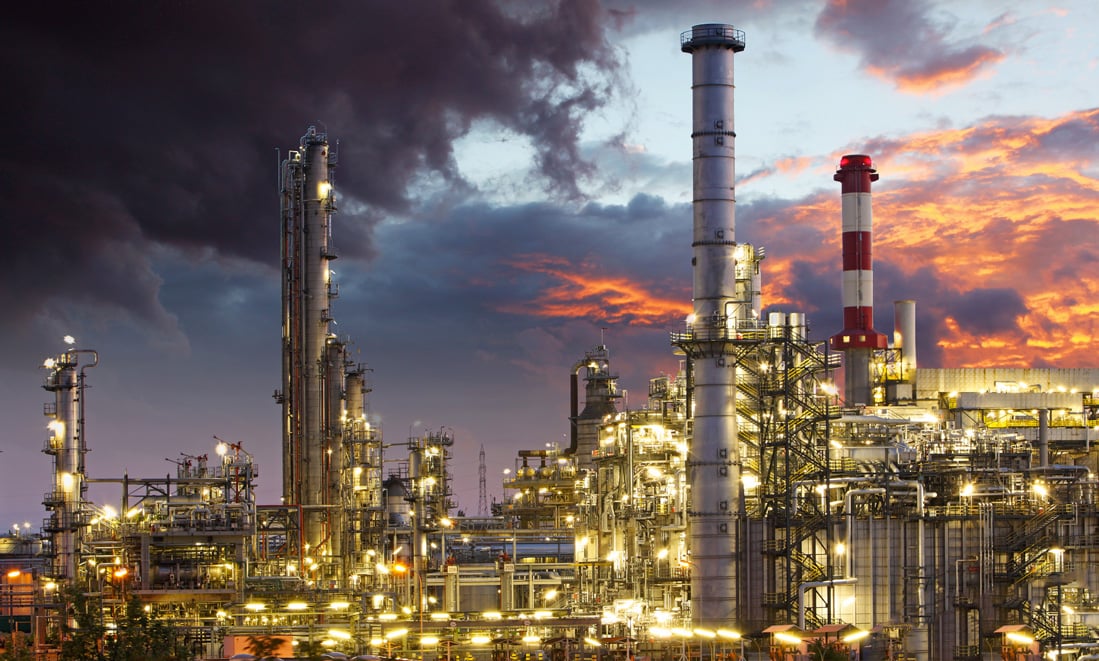

The best course for safety traditionally lies in ensuring people are located far from hazards. Unfortunately, there are instances when that is not possible. Oil and gas refineries are one such work site; chemical facilities, power generation, military installations, and research laboratories are a few others. Blast-resistant buildings protect those who must work close to these hazards. They may be temporary or permanent structures, but they are present due to the potential for saving lives and protecting valuable assets should a catastrophic event occur.
Blast-resistant buildings are designed to withstand various hazards, including blasts, thermal loads, and toxic releases. Their modular construction allows for quick and efficient installation, making them an ideal choice for industries requiring rapidly deployable solutions and as little time spent in hazardous areas during installation and construction as possible.
Blast-resistant modular buildings have many benefits and require careful design considerations to ensure their safety and effectiveness. In this article, we'll explore some critical factors for design considerations of blast-resistant modular buildings and provide valuable insights into the design considerations necessary to protect you (or your team) and your assets.
Hazards Identification Process
Before a blast-resistant building is ever placed on a hazardous work site, the site will need to be evaluated. This process involves conducting a thorough study to determine the potential risks that could impact buildings, occupants, and surrounding areas. The process is typically reviewed every five years.
There are two schools of thought in identifying hazards. There are consequence-based studies that consider the potential consequences of a threat and risk-based studies that evaluate the likelihood of a hazardous event and then look at its potential consequences. The choice of method typically depends on the specific goals and circumstances of the project.
One type of analysis is a Facility Siting Study, which should be done every five years on oil and gas refineries as part of their OSHA Process Hazard Analysis (PHA) or every time a process changes.
Another example is Quantitative Risk Assessments (QRAs). A QRA is a risk-based study that quantifies the highest priority risks. This study will contain all of the information in a facility siting study but is a more comprehensive, advanced analysis. The QRA can also be used to fulfill the OSHA requirement that comes up every five years in the PHA.
A facility siting study, which is less costly and quicker to perform, is based on Maximum Credible Events (MCEs). Because the results tend to be conservative, that could impact the cost of modifying existing occupied buildings or adding future-occupied buildings.
The extra element QRAs have that facility siting studies don't, is statistical probability. The statistical probability helps remove some of the conservatism and allows companies to make decisions based on risk tolerance. While facility siting studies and QRAs both serve a purpose, most larger companies and facilities will benefit from the risk-based analysis, the QRA.
Once hazards are identified, solutions to protect workers from potential risks are suggested. Solutions to mitigate hazards might include:
- Suggestions to move non-essential personnel to non-hazardous areas.
- Adding permanent blast-resistant structures.
- Retrofitting existing structures to meet the threat level.
- Bringing in temporary blast-resistant buildings.
Be cautious of this process if the one and only solution identified is the solution that the firm doing the analysis sells. (More on this later.)
Not Every Site Requires Multi-Hazard: Designing for the Threat Level Identified
Blast-resistant buildings come in all sizes, varieties, and types of materials. They may be steel, concrete, modular, built on-site, permanent, temporary, or a combination of these selections. Once the threat level is identified through a QRA or FSS, you can mitigate hazards.
At RedGuard, our philosophy involves creating a solution tailored to a customer’s needs. We start with steel modular, blast-resistant buildings, which can have a protection level of up to 15 psi. We then add other protections, as needed. (The add-ons and protections mentioned in this post are available on all RedGuard custom BRBs.) Other companies may have a catchall approach and suggest mitigating with “multi-hazard” buildings. While a multi-hazard approach ensures protection, it may not always be the most appropriate strategy. A risk-based approach that carefully assesses the actual threats relevant to the location would typically lead to a more efficient, cost-effective, and tailored solution.
It may seem like a great idea to use these "catch-all" multi-hazard buildings in all areas that require threat mitigation, but that can create additional issues, like:
- Increased costs due to additional specialized materials, engineering, and construction.
- Increased weight, which is primarily a concern with concrete buildings. They are substantially more expensive to ship and handle, due to weight. The larger the building, the more difficult they are to handle and ship.
- Over-engineering, which can lead to inefficient use of materials and resources.
- More complex maintenance. If some of these systems are unnecessary, they must still be maintained, leading to extra costs and possible complications.
- More space utilization. Additional protection measures may require additional space or impose limitations on the layout of the building. This could hinder the optimal use of space or compromise other functional aspects of the building.
Blast Considerations in Hazardous Areas. Do You Need Multi-Hazard?
As mentioned, ensuring the safety and effectiveness of blast-resistant modular buildings is crucial. That means considering both structural and non-structural design. At a minimum, new buildings should be designed to the threat level identified in the PHA. Sometimes, a building’s capacity will be increased to compensate for future changes.
There are several factors to consider during the design phase of blast-resistant modular buildings. Understanding these considerations can ensure the structural integrity and resilience of the buildings, ultimately safeguarding workers' lives and protecting valuable assets.
Structural Considerations - SDOF Method (Single Degree of Freedom):
Some studies will apply the Single Degree of Freedom (SDOF) method in the structural analysis of blast-resistant modular buildings to determine the dynamic response of the structure to blast loads. The degree of freedom refers to the number of independent parameters or variables that describe the motion or behavior of a system. It assumes that the entire structure responds as a single unit. It considers the building a single degree of freedom, characterized by mass, stiffness, and damping properties. This method is a simplification technique used in structural analysis to represent the overall behavior of a building subjected to blast loads. Its conservatism has made the SDOF method a tried and true way to look at onshore applications.
An example of a single degree of freedom would be a blast-resistant building that would normally be rated for 8 psi, but has a window that is only rated for 5 psi. The lower psi rating for the window lowers the blast rating for the whole building since the building is considered a single unit. If the building was subjected to a blast higher than 5 psi, the lower-rated window could potentially become a weak point or a point of failure, compromising the integrity of the entire building.
Structural Consideration - Finite Element Analysis (FEA):
For blast-resistant modular buildings in offshore environments, or if weight is a consideration, Finite Element Analysis (FEA) is a valuable tool in the structural design process. FEA allows for a detailed analysis of the complex interactions between the building, its supports, and the surrounding environment. By simulating the impact of blast loads and structural response, engineers can optimize the strength and durability of the design and identify potential weak points that require reinforcement.
Structural Consideration - Independent Field Testing:
When designing blast-resistant modular buildings, it is crucial to work with a reputable manufacturer that has validated its designs through rigorous third-party testing, rather than solely their own labs, testing, and engineering teams. Blast tests and structural simulations provide empirical evidence of a building's performance under hazardous conditions.
Using third-party engineers for testing, rather than in-house engineers, brings an independent perspective to the analysis process to identify potential blind spots or biases in the manufacturer’s internal testing. Since a third-party engineer will have no vested interest in the outcome, they provide an extra layer of accountability and transparency.
Non-Structural Design Considerations - What’s Inside Matters:
Safety in a properly designed blast-resistant building also means considering non-structural components. Non-structural components include items like partitions, ceilings, HVAC systems, piping, electrical systems, and equipment. During a blast event, the blast wave and resulting vibrations can cause these components to detach, become projectiles, or create hazards within the building. By considering their design, placement, and how they are secured, the risk of injury to occupants can be minimized. Material selection and installation technique is critical.
Thermal Considerations for Steel BRBs
Thermal threats in a petrochemical facility typically result from high temperatures and exposure to flames or hot gases. These threats can cause significant damage to infrastructure, equipment, and personnel. Steel blast-resistant buildings are designed to mitigate some of these threats inherently, while other protections can be added, depending on the identified threat level. Steel blast-resistant buildings can protect against explosions, fire, and extreme heat. Here's a detailed look at the thermal threats and how blast-resistant buildings can mitigate them:
1. Risk of Fire on Oil and Gas Sites
Petrochemical facilities process and store flammable substances, creating a high fire risk. These threats are mitigated through the use of fireproof materials that will contain a fire, preventing it from spreading to other parts of the facility. Fire suppression systems can be integrated to detect and suppress a fire quickly.
2. Extreme Heat
High temperatures from processes or accidental events (like fires) can weaken or damage equipment and structures. Construction with materials that resist deformation or weakening at high temperatures can safeguard against this threat. Proper insulation helps maintain temperature within controlled limits, protecting people and equipment. Integrated cooling systems can keep temperatures safe during normal operations and emergencies.
3. Flash Fires
A flash fire is a rapid-moving flame front that can sweep through an area, especially in a confined space with a rich fuel-to-air mixture. RedGuard’s blast-resistant buildings are meticulously engineered to withstand flash fires without the need for additional protection. We prioritize the safety of occupants and the preservation of assets with our robust design and construction techniques that can endure the intense heat and pressure generated during flash fires.
4. Jet Fires
A jet fire is a turbulent diffusion of flames resulting from the combustion of a flammable gas escaping under pressure. For areas at risk of jet fires, RedGuard employs an advanced intumescent coating.
An intumescent coating is engineered to provide extended protection against jet fires and other severe thermal events. They are rigorously tested and certified to ensure they can withstand the specific conditions they are designed for, including high-velocity flames and intense heat, applied for specific time frames. Adding these high-performance intumescent coatings to steel blast-resistant modular buildings can provide an extra layer of safety, ensuring that the building and its occupants remain protected despite the most extreme thermal threats.
Toxic Considerations in Blast-Resistant Buildings
In environments where toxic materials are present, it’s paramount to the safety and well-being of personnel to consider what would happen in the event of a toxic release. Various methodologies and strategies can be employed to combat the potential release of hazardous substances.
1. Typical Methodologies for Combating Toxic Releases
Containment Systems are designed to prevent the spread of toxic substances. These systems may include barriers, secondary containment, or specially designed storage areas.
Emergency Response Plans should outline procedures for mitigating and responding to toxic releases. These plans should include evacuation routes, communication protocols, and designated assembly points.
Personnel Training on how to respond to toxic releases should include proper use of personal protective equipment (PPE) and emergency response protocols.
2. Basic Shelter-in-Place Strategy
One common approach for protecting occupants of blast-resistant modular buildings during a toxic release is the shelter-in-place method. In this method, occupants work inside a building that is a shelter. If a toxic gas release occurs, they are instructed to stay inside the building and seal off all external openings, such as doors and windows, to minimize the infiltration of toxic gases.
To facilitate the shelter-in-place strategy, blast-resistant modular buildings can be equipped with airtight seals and ventilation systems that seal off in an emergency. Occupants should have access to emergency kits containing respirators and other necessary safety equipment.
3. "Safe Haven" Strategy
Sometimes, it may be necessary to design a blast-resistant modular building to be a "safe haven" rated structure. A safe haven is a specially designed and fortified area within the worksite that provides the highest level of protection against toxic releases and other hazards. In an emergency, workers are instructed to go to this specialized area.
Key features of a safe haven-rated building may include reinforced walls, specialized ventilation systems, emergency power sources, and advanced filtration systems to ensure that the air inside remains safe to breathe even during a toxic event. These areas are typically designed to accommodate occupants for an extended period until they can safely exit.
4. Incorporating HVACs with Purge and Pressurization Systems
To minimize the infiltration of toxic gases and ensure a clean air supply, blast-resistant modular buildings can incorporate HVAC systems with purge and pressurization capabilities. These systems can create a positive pressure environment that prevents the entry of contaminated air.
Purge and pressurization systems are particularly effective in environments with potential toxic gas releases, as they maintain a controlled and safe indoor atmosphere even when hazardous conditions exist outside the building.
HVACs with these systems can be incorporated into shelter-in-place or safe havens.
5. Addition of Gas Detection Systems
To provide early warning and real-time monitoring of toxic gas concentrations, blast-resistant modular buildings should be equipped with gas detection systems. These systems can detect the presence of harmful gases and trigger alarms or ventilation systems to respond accordingly.
They can be integrated with the building's HVAC and automation systems to automatically initiate safety protocols when elevated gas levels are detected. Regular maintenance and calibration of these systems are essential to ensure their reliability.
Multi-Hazard that works for you: Tailored Safety for a Complex World
Safety isn't a one-size-fits-all endeavor. It's a dynamic, multifaceted challenge that demands thoughtful consideration, adaptability, and precision. While some companies lean toward bundling multiple hazards under a single "multi-hazard" umbrella, a more nuanced approach emerges when we truly delve into the complexities of safeguarding lives and assets in hazardous zones.
There is a fundamental truth among blast-resistant buildings: the most effective safety solutions are tailored to the location’s unique risks and challenges. In hazardous zones, this tailored approach is a beacon of security.
First and foremost, the process begins with a meticulous Hazards Identification Process, distinguishing between consequence-based and risk-based methodologies. Here, we lay the foundation for an effective safety strategy, understanding the nature and magnitude of potential threats.
But the wisdom to discern between necessary protection and over-engineering is what sets a truly resilient safety strategy apart. Instead of investing in the broad strokes of a "one size fits all" multi-hazard approach, we advocate for precision. Tailor your safety measures to the specific threats, and allocate resources where they really matter. This approach ensures that blast-resistant modular buildings are robust, yet efficient. It's about constructing fortifications that don't compromise safety while optimizing resources.
To discuss your mitigation plan for hazards on your worksite, contact RedGuard. You can use the link below to email us and set a meeting with the writer of this blog post, Phillip Lange.
Phillip Lange
Phillip Lange is the technical sales manager at RedGuard. With his experience working with companies in the oil and energy industry, his specialties include process scheduling, negotiation, budgeting, value engineering, and operations management. He oversees technical engineering services that are offered at RedGuard, like facility siting studies, building retrofits and custom blast-resistant solutions.