The petrochemical industry is rapidly responding to the fact that too many blast zones contain buildings that can’t withstand a blast. While some companies are still trying to tackle the problem with traditional construction methods, there is a widespread movement toward the use of modular, metal buildings because of their proven ability to protect personnel.
Now we’re seeing a new phase in this evolution of thought: a hybrid structure combining the toughness of modular buildings with the amenities of permanent construction. The biggest advantage of a permanent structure is the comfort and appearance of its interior, and now a new line of blast-resistant buildings (SafetySuite by RedGuard) offers the best of both worlds.
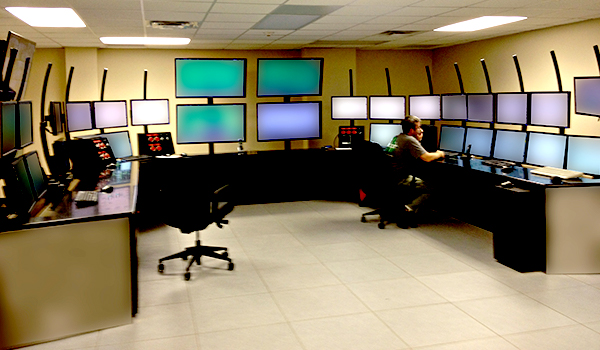
Protection, comfort ... and then some
When RedGuard started making blast resistant buildings in 2005, the company used shipping containers as the structural model because containers had survived where traditional buildings had not in the blast zone of the Texas City, Texas, refinery disaster earlier that year. Then RedGuard blast tested its design to confirm not only would the building survive but its occupants would also be protected.
A modular building is tough, functional and fills a variety of needs, from guard shacks to tool cribs, but some applications call for the amenities of a traditional building interior and the psychological familiarity of a permanent structure. This is how the SafetySuite concept was born. This new blast protection design offers interior drywall, drop ceiling options and foundation mounting.
And a SafetySuite usually costs about half as much as its traditional building counterpart.
Permanent but not too permanent
The fact these buildings are mounted on foundations doesn't mean things can’t change when a facility’s needs change. At its heart, a SafetySuite is still a modular design, which makes it simple to dismantle and relocate compared to a fixed facility that has to be torn down when a company expands or redesigns its site configuration.
The SafetySuite’s modularity also makes interior changes simple. If you need more space, you can add another module. If you need more restrooms or an additional control room, you can drop new sections in with an ease traditional construction doesn’t offer. It’s also worth noting RedGuard’s temporary lease buildings can come in handy during the transition while a SafetySuite is being moved or modified, keeping personnel blast protected on a continuous basis.
A simpler approach
The construction process has always included a collection of “necessary evils” to which RedGuard no longer has to resign itself. For example, long interruptions to operations are a thing of the past. Because a modular building is constructed mostly off site, it’s a simple matter of bolting it to a foundation, connecting its sections and hooking it up to plumbing and electricity when it reaches its destination. Less on-site construction means less inconvenience and downtime.
It can also be a bonus that no welding must take place on site when a modular building is erected, which avoids safety risks that may require a shutdown of surrounding operations.
Built for petrochemical
RedGuard believes in bringing clients in early during the design stages to help them understand the range of possibilities provided by modular construction. RedGuard’s team of designers, drafters and estimators is able to provide quick, accurate answers about options and costs while adhering to best engineering practices for blast protection. Because of RedGuard’s deep experience in the petrochemical industry, it can often help companies anticipate future needs, then work with them to design buildings that will meet those needs.
The biggest convenience is the turnkey nature of modular construction. It’s a seamless solution unburdened by many of the extraneous costs associated with traditional construction, and its low overall price tag leaves plenty of margin on the table for companies that spec them into petrochemical operations.
Tougher, cheaper, easier and now more attractive; it’s not often you run into a combination like that.
Jeff Lange
Jeff Lange, now a managing partner for LANGE, the parent company of RedGuard, founded the company as ABox4U in 1998. It was originally a portable storage company, and through the years has been rebranded with a specialty in creating blast-resistant buildings for oil and gas companies. He saw an early need to focus on safety and made it a passion to create products that save lives. With a strong leadership team at RedGuard that oversees day-to-day operations, he remains a managing partner at RedGuard and several other divisions of his LANGE company.