Design & Engineering | Industries | Blast Resistant Buildings | Hazard Protection
Enhancing LNG Plant Safety with Steel Modular Blast Resistant Buildings
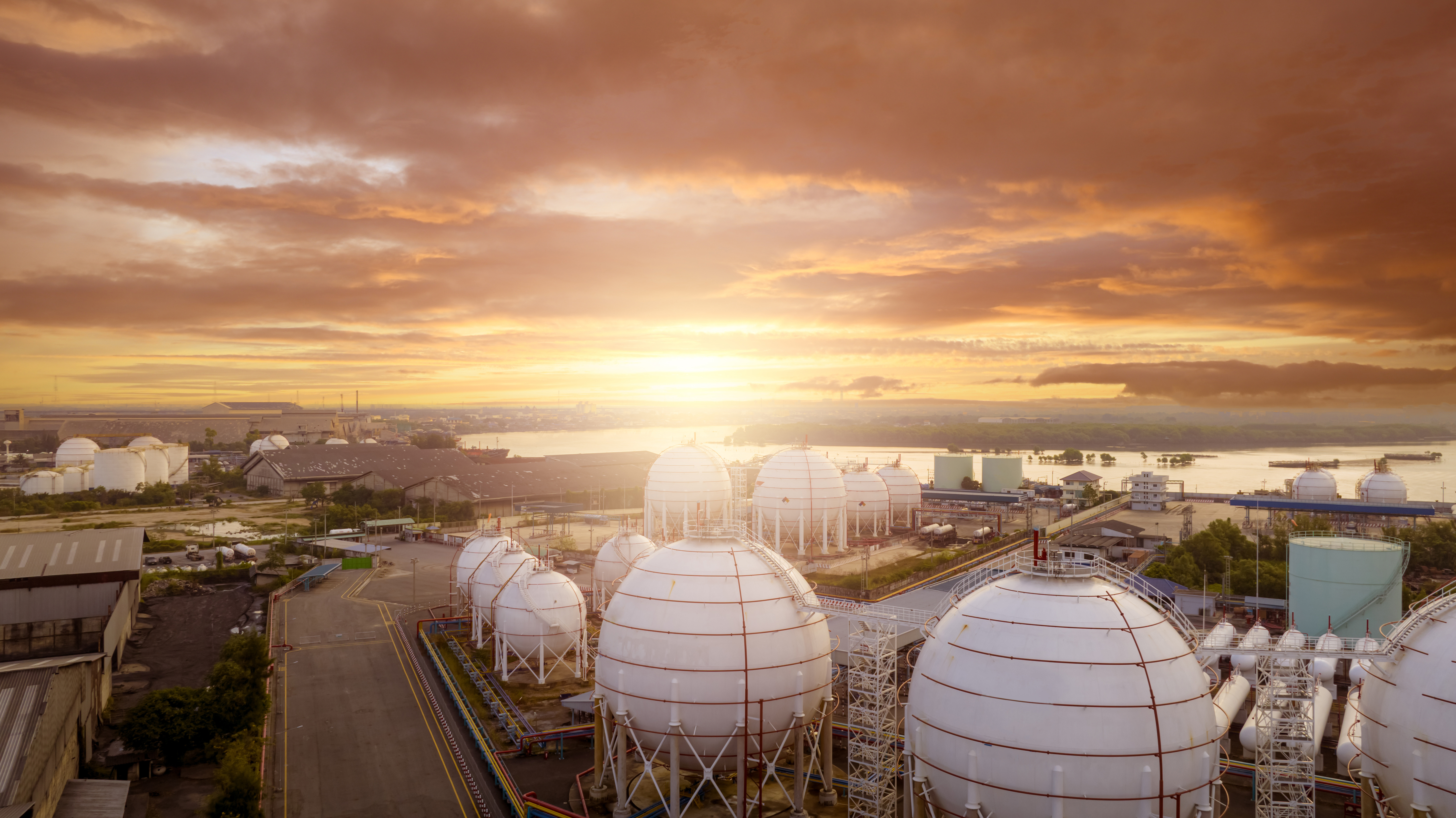

As this article is being written, there are six new LNG (Liquified Natural Gas) plants under construction in the US and two more in Canada. There are dozens more under consideration or awaiting approval before the Final Investment Decision (FID) is made. Safety and efficiency come first in energy production, an industry that encompasses the processes and infrastructure involved in generating, converting, and distributing energy to meet society's ever-demanding needs.
LNG plants, which convert natural gas into liquid form for easier storage and transportation, are particularly challenging environments due to the high-risk nature of their operations. LNG can be volatile if leaked into an air-gas mixture. That volatility demands robust safety measures, and one of the most promising innovations in this field is the use of modular blast-resistant buildings. These structures are reshaping how safety is managed in LNG plants, combining modular design principles with blast-resistant technologies. RedGuard is leading the way in this burgeoning industry with its blast resistant solutions.
Understanding the Need for Blast-Resistant Buildings
The risks at an LNG plant are significant. The plants operate under high pressure and handle flammable materials, posing significant safety risks. The potential for explosions and fires calls for rigorous safety standards and protective measures. Traditional construction methods rely on static, non-modular buildings that are either costly or time-consuming to construct and are difficult to modify. Modern LNG plants prioritize speed to market, and their operational needs can frequently change. All these factors mean there’s a growing demand for flexible solutions that can keep up with the rapidly shifting operational needs.
That’s where steel blast-resistant buildings come in. They are designed to withstand explosions and mitigate damage from blast waves. They incorporate rugged materials and construction techniques that enhance their ability to absorb and dissipate explosive energy, protecting both the structure and its occupants. Prefabricated off-site and assembled on location, they offer a unique blend of safety and flexibility—a perfect match for the dynamic demands of an LNG plant.
Five Advantages of Steel Modular Blast-Resistant Buildings
- Enhanced Safety through Innovative Design
Modular steel blast-resistant buildings are engineered with reinforced heavy gauge steel, and blast-resistant glass, among other features. The robust materials and modular designs provide superior protection against explosions. Unlike traditional methods, the modular approach seamlessly integrates these safety features. RedGuard building designs have been blast-tested to prove the efficacy of our structures. Blast calculations and structural drawings are a critical part of every SafetySuite, RedGuard’s line of custom blast resistant buildings. - Flexibility and Scalability
Operational requirements can change rapidly at LNG plants. Modular buildings can be easily reconfigured or expanded to accommodate new functions or processes. This flexibility is particularly useful for LNG plants, which may need to adapt their facilities for higher production, to incorporate new technologies or respond to changing regulatory requirements. Unlike traditional buildings, which require extensive renovations or new construction, modular buildings can be modified with minimal disruption to ongoing operations. - Faster Construction and Reduced Costs
One of the most significant benefits of modular construction is the speed that buildings can be installed after delivery. Prefabrication in a controlled factory environment allows for more efficient use of materials and labor, leading to faster completion times. In the context of LNG plants, where downtime can be costly, modular buildings reduce the time needed for construction and minimize operational interruptions. Additionally, the reduced on-site construction time lowers overall project costs and reduces the risk of delays. - Quality Control and Consistency
Modular buildings are constructed in a factory setting where quality control is more easily managed than traditional on-site construction. This controlled environment ensures that each component of the modular structure meets high standards for safety and performance. This consistency is invaluable for LNG plants because precision and reliability are a must. While our blast-resistant design is third-party tested for safety, each unit is also subject to a Factory Acceptance Test for quality. This happens before transporting it to the site to ensure that the final assembled structure meets all quality, safety, and performance criteria. - Environmental and Sustainability Benefits
Modular construction often produces less waste and a smaller environmental footprint than traditional building methods. Prefabrication allows for more precise material use and reduces the amount of construction debris. Additionally, modular buildings can be disassembled and relocated, which extends the lifecycle of the materials used, a common sustainability goal. In the context of LNG plants, where environmental impact is a significant concern, these benefits contribute to more sustainable operations.
Implementation in LNG Plants
Adopting steel modular blast-resistant buildings in LNG plants is becoming increasingly common. These structures are used for a variety of purposes, including control rooms, operator shelters, guard facilities, switchgear/MCC enclosures, and much more. The ability to deploy these buildings quickly and safely makes them ideal for use in high-risk environments with multiple threats, like fire, gas or blast. Moreover, as LNG plants continue to expand and evolve, the modular approach offers a scalable solution that can adapt to changing needs.
In the construction of a new LNG facility, modular blast-resistant buildings can be put in place quickly, often in parallel with other critical plant components. This approach streamlines the project timeline and ensures that essential infrastructure is ready without the delays associated with traditional construction methods. As LNG plants undergo upgrades or expansions, modular units can be added or reconfigured with minimal impact on existing operations.
Steel modular blast-resistant buildings represent a significant advancement in the construction and safety management of LNG plants. By combining the latest in blast-resistant technology with the flexibility of modular design, these buildings offer a solution that meets the demanding requirements of modern LNG facilities. They provide enhanced safety, faster construction, and adaptability, all while supporting sustainability goals. As the LNG industry continues to grow and evolve, RedGuard steel modular blast-resistant buildings are poised to play a crucial role in ensuring safe and efficient operations, setting a new standard for construction in high-risk environments.
For more information about RedGuard’s modular solutions for LNG facilities, set up a brief discovery call with our specialist.
Dean Alcott
Dean is the Market Development Manager for RedGuard and he has more than 25 years of experience with specialty modular structures. He has been heavily involved in transforming RedGuard from company that did business only in North America, to a global leader in the manufacture and supply of safe space.