Compliance, Safety and Best Practices for Blast-Resistant Buildings
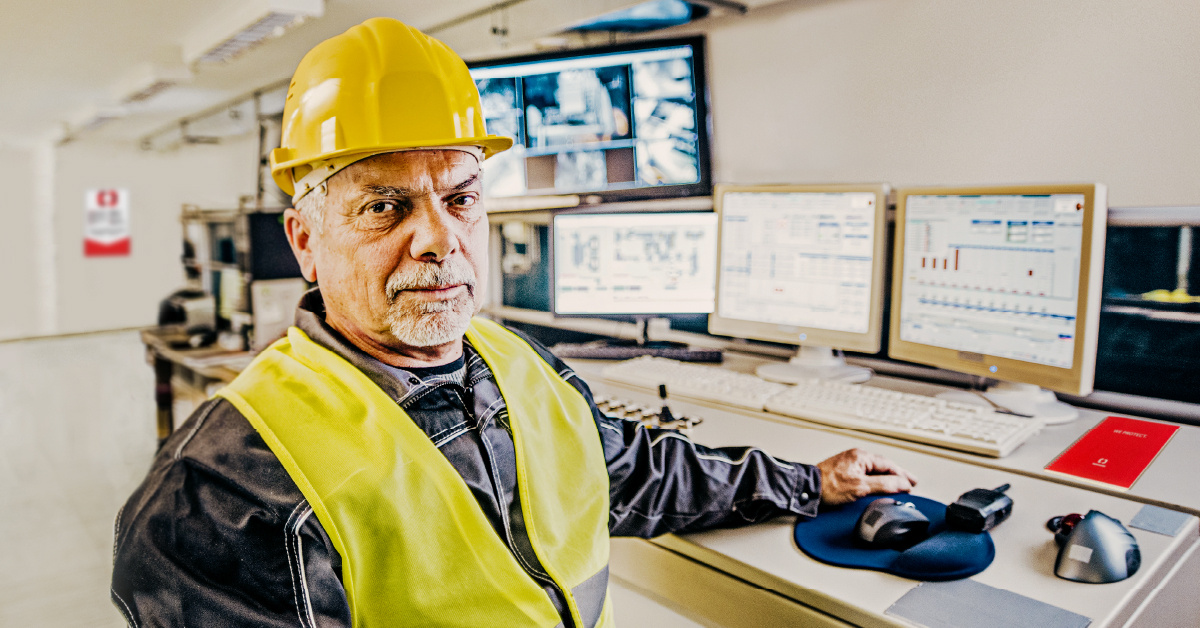

This article was originally published for RedGuard in the November/December 2024 issue of BIC Magazine. It was written by David Ellerman, one of RedGuard's subject matter experts and our Regional Area Manager in the Great Lakes Region.
Modular blast-resistant buildings play a crucial role in daily operations within the petrochemical industry for both temporary and permanent uses. These structures are used as control rooms, labs, admin buildings or temporary facilities for maintenance turnarounds. The petrochemical industry relies on blast-resistant buildings to meet safety and threat mitigation needs and protect personnel working in hazardous areas. While there are no official regulations for blast design, engineering best practices are outlined in API Recommended Practices 752 and 753 to guide both temporary and permanent structures, with the latter requiring more scrutiny. Permanent structures follow guidelines like conventional construction.It is crucial to the success of a modular project to understand the entire approval process for permanent buildings. However, navigating this can be challenging, as there are no specific codes or regulations for modular buildings in the U.S. Licensed manufacturers and builders are required to adhere to all applicable building codes for the building’s geographical location. It's wise to understand guidelines dictated by the state, local authority having jurisdiction (AHJ), third-party engineering plan review and specific code requirements of the geographic location. Adhering to these guidelines is a step toward a building that meets compliance criteria and can be successfully permitted for occupation.
Several agencies may come into play. The International Code Council (ICC) is a nonprofit standards organization. It has developed the International Building Code (IBC) which should not be confused with the Interstate Industrialized Building Commission (IIBC). Because we are talking about modular units, there is also the Modular Building Institute (MBI).
There is minimal difference in compliance between traditional construction and modular as the latter must comply with the same state-adopted version of the IBC. In the early planning stages, it's important to consider state and local codes, manufacturer compliance with state regulations, inspection and permitting processes, code adoption cycles, IIBC states and ICC/MBI standards.
Navigating this is difficult if you’re unfamiliar with the requirements. During the planning phase, your selected vendor should provide guidance. However, additional references are available. Most states participate in an industrialized unit and modular building program. Including your local AHJ for local requirements is also beneficial. The ICC/MBI standard for off-site construction, ICC/MBI 1200-2021,1205-2021 and 1210-2023, was published in 2019, and the use of modular buildings has only increased since then. These documents were published as a guideline for meeting the minimum requirements to address safety and compliance. However, the process can vary depending on the state and local municipality.
Modular buildings need to adhere to state IBC design requirements. Third-party review is often required after engineering, with inspection timing varying according to state or local requirements. Nine states do not have modular building programs and rely on local AHJs.
The IIBC aims to endorse states' mutual recognition of IBC modular building programs using standardized guidelines. Some states require additional fire marshal review, while others need approval letters before construction. Certain states don't allow third-party review, while others allow it but not third-party approval. Several states require a manufacturer's license to build and deliver modular buildings, and some also need a retailer license to sell them.
Before leaving the manufacturing facility, modular or industrialized buildings must often undergo state or third-party inspection before approval for delivery. A state-issued label indicates that all factory-built elements comply. While this list is not complete, there are benefits to understanding the process and requirements before the execution of a project. Following the proper procedures and adherence to guidelines for a specific geographic location will ensure the issuance of the required permits to complete construction and occupy the building.
Modular building construction is gaining ground as an alternate method to conventional construction. Industry analysis from the MBI shows that market share and revenue are expanding into new markets. The off-site modular industry has progressed into a “building delivery system.” Large building sections can be done entirely in a factory setting and delivered to the destination. This provides a competitive advantage through decreased costs, quicker construction lead times and minimal disruption to the site’s daily operation. With continued growth, the requirements evolve similarly to how code requirements change every few years. This dictates a thorough understanding of the processes with the ultimate goal of compliance.
For more information, visit RedGuard online or call (855) 733-4827.
David Ellerman
David Ellerman is the Regional Area Manager of the Great Lakes Region for RedGuard, and he's also worked in project management for the company. He's been with RedGuard since 2016 and served in the United States Army. David holds a Master's Degree from the Missouri University of Science and Technology.