Choosing the Safest Materials for Hydrogen Operations
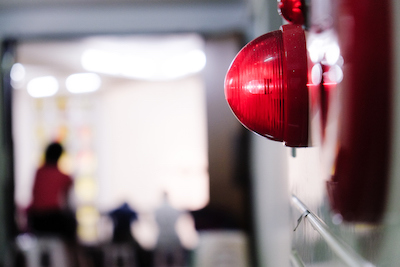

Interest and demand in the hydrogen industry are both on the upswing. In 2020, energy companies produced roughly 50 million tons of hydrogen, and it's estimated that by the year 2050, production could increase to 500 million tons.
Currently, there is around $80 billion invested in the industry, so those looking to tap into its potential will need to find safe ways to process, transport, and store it. That's where steel blast-resistant buildings come in – they are strong and portable enough to adapt to emerging and fast-paced needs.
Working With Hydrogen
Hydrogen is a highly reactive substance. Its potential for combustion, when not handled properly, and its broad flammability range cause some people to hesitate. But as a critical piece of the clean energy puzzle, hydrogen production shows no signs of slowing. It's a challenging element to work with, but safety standards have come a long way.
In the event of an explosion, hydrogen can produce high blast loads. It's also more likely to undergo a deflagration-to-detonation transition (DDT) compared to traditional fuels. These explosions can have supersonic flame speeds and substantial overpressures (aka blast waves) of roughly 294 mph. That's enough to demolish a reinforced concrete building, scattering pieces around a worksite.
It's clear that any on-site building must have thick walls to absorb the pressure of high blast loads in a way that minimizes damage to the building while preventing dangerous hydrogen leaks, protecting the safety of people and equipment.
How to choose the safest material for your hydrogen operation
In potentially dangerous environments like hydrogen plants, having a well-designed, properly sited control building is a critical piece of maintaining or regaining control during an event. RedGuard’s blast-resistant control rooms are made of strong, non-combustible construction materials like steel.
To keep the area safe, the control room must have a robust structural response and limit blasts to reduce non-structural debris that can injure personnel onsite. However, that also makes windows and doors a potential liability, so structures need to be adaptable and custom-built for each use.
A structure should be able to be shipped to locations near processing, storage, or handling areas, and site managers need to look for companies with worldwide teams that can help construct and inspect the final product. RedGuard’s modular structures can be relocated and further optimized later, while most concrete structures are immovable by nature once they are placed onsite.
Building the hydrogen operation facility you need
Portable blast-resistant buildings are the key to keeping workers safe. RedGuard buildings don't need to rely on sales talk. Instead, we've worked with third-party engineering firms to conduct our blast tests using buildings rated from 7.5 psi to 9.9 psi, all of which stood up to the challenge. It's crucial to ensure that the buildings match up to their response level ratings when you know workers' lives are on the line.
The strength, stability, and flexibility of steel all make it the perfect material to use in blast-resistant modular buildings, especially on sites that handle volatile elements like hydrogen. With RedGuard's building design services and off-site production, work at your facility doesn't have to stop for lengthy building construction.
Our team of professionals knows what our buildings are capable of and can guide you in designing a facility that not only protects your product but your most critical onsite assets – your people.
RedGuard Sales & Marketing
The RedGuard sales and marketing team curates and writes on a variety of topics regarding blast-resistance and modular buildings. To inquire about any of the topics you read about on our blog, connect with us.