Service & Maintenance | Field Service
From RedGuard Service: Blast Resistant Building Door Maintenance
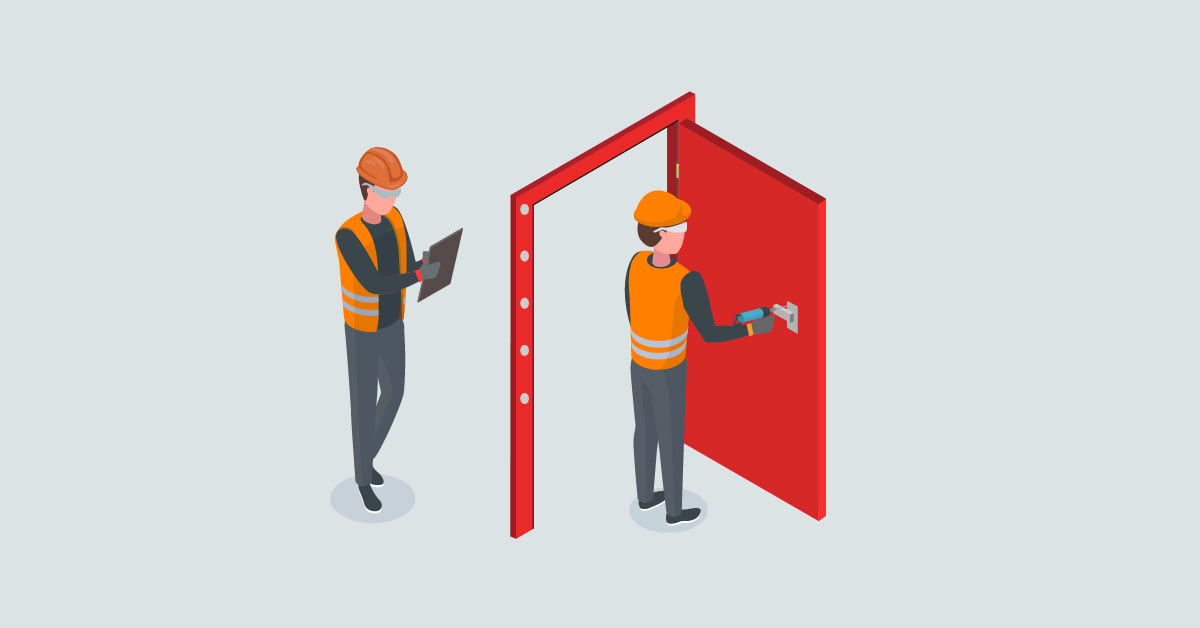

When it comes to weight, the doors on a blast resistant modular building (BRM or BRB) tip the scales around 600 pounds. When they are on customer sites like refineries, nitrogen or olefin plants, or other hazardous sites where blasts could occur, they receive more wear and tear than their occupants may realize. The weight of the doors and the number of times they are opened and closed during a 12-hour shift impact the amount of routine maintenance that should be given to them. For example:
- In a galley or dining room, the doors may only be opened and closed between a hundred and two hundred times per shift.
- A permit office may have a door, or doors, that open and close one thousand to fifteen hundred times each during two 12-hour shifts.
- A normal office may only have a door, or doors, open and close fifty times per shift.
The door is made up of three major components:
- The door itself
- The door handle
- The door’s hinges
Maintenance for blast resistant doors begins with “Look, listen, and feel.” For example, when reviewing the operation of a BRB door, you will want to look at the following:
- Watch and pay attention to the door. Observe how the door itself opens and closes and how easily it operates.
- Is it hard to open?
- Is it difficult to close?
- Is there light showing through, at the edges, when the door is closed?
- Does the door drag on the threshold?
- How does the door handle feel and operate?
- Does the latch operate properly?
- Does the door handle feel loose or too tight?
- Does the handle latch not catch properly and keep the door shut?
- Check the locks and make sure they are operating correctly.
- How do the door and hinges sound and feel when opening or closing
- Is there any noise coming from the hinges?
- Are there any grinding or steel-on-steel “screech” sounds in the hinges?
- Is there a dragging feeling that seems to come more from the hinge operations than the door itself?
If any of those occur, you will need to call a service order in and have a service technician come and address the issues with your blast resistant door.
If there are no issues, you still need to maintain the door. In the preventative maintenance of a BRB's doors, the tools you will use are as follows:
- Phillips-head screwdriver
- Flat-head screwdriver
- Clean rags
- Lithium grease
- Lightweight oil
At least once a month for standard-use doors (like an office or a dining room), you should perform the following:
- Grease the door hinges at the grease points, and be sure to use the right kind of grease in them. If in the Gulf Coast, marine-grade grease is recommended, and in other locales, a white lithium-based grease is suggested.
- Clean the door locks with a damp rag, and do not use chemical cleaners. Chemical cleaners have abrasive materials that will wear down the mechanisms over time.
- Make sure to lubricate and oil but not over-oil the door latches and catch mechanisms.
- If or when possible, spray a dry lubricant into the keyways and then clean out any debris with the key.
- Lubricate the locks lightly to ensure the keys will insert easily and move freely with the key. While it is inserted, turn to lock, and then unlock the mechanism.
Remember, no matter its use, the more it is opened and closed, the more a door will need to be maintained. If you do not perform maintenance, it will break down. Nothing lasts forever; a broken door is difficult to deal with and can quickly become a safety hazard.
A broken door obstructs the operations of your personnel and unit. It could cost the company more money to replace it than to maintain the door, especially if you have to block access to the BRB. Blast resistant buildings are in place for a reason, and if the door doesn’t operate or shut properly, it won’t protect the occupants of the building, by preventing a blast from entering the building.
For more information, or to get service from the RedGuard service team, contact us today!
Adam Crocker
Adam Crocker is the field service manager at RedGuard and has been at the company since 2019. Both his previous time serving the petrochemical industry and his military background gives him a unique understanding of the industry and has kept the RedGuard service team operating smoothly. His goal is to keep his team operating safely and professionally while delivering efficient service to customers to keep their operations running safely.