Articles | Best Practices | Custom Buildings
Technical custom-building projects don’t have to be a nightmare
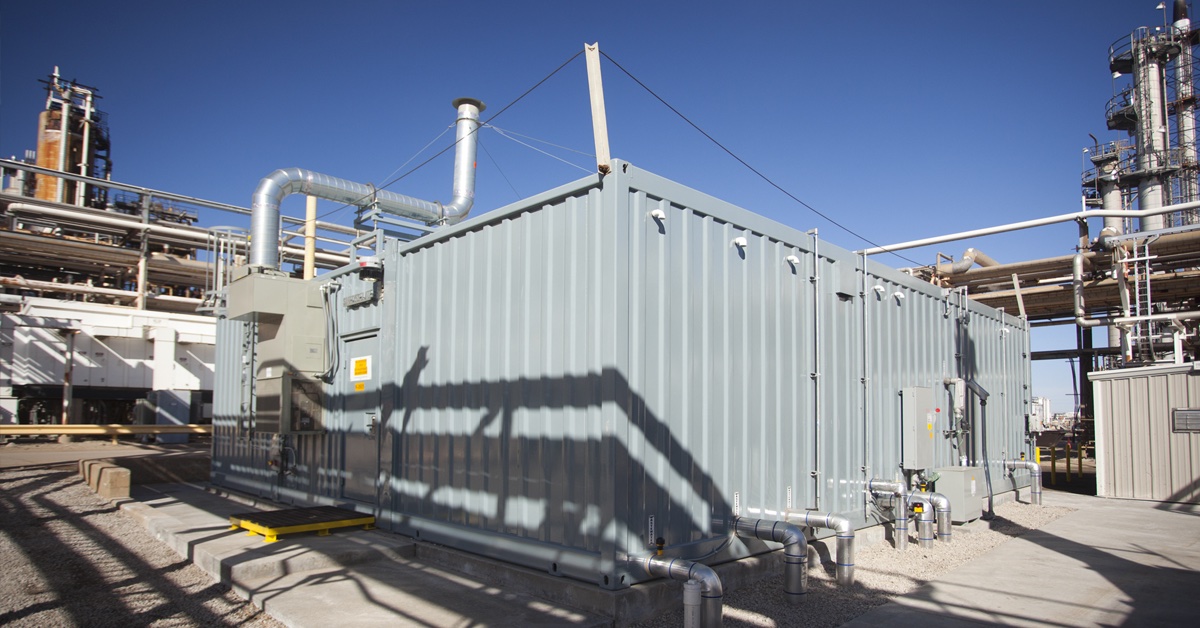

This article was originally published in the November/December 2023 issue of BIC Magazine. It was written by Bryan Bulling, RedGuard's Northeastern Director of Sales.
Finding an example of a place where technological advances haven’t taken giant leaps is nearly impossible. Without making an effort to keep up, you risk falling behind.
RedGuard’s proven design and engineering have influenced decision-making in multiple industries. Our SafetySuite line of custom modular hazard-resistant buildings, also known as blast-resistant buildings, have driven this change. Evolving segments, like renewable energy, drive interest in rapid deployments and technological advances enable it to fabricate and construct safe buildings in hazardous zones.
At RedGuard, we recognize the importance of front-end design and focus on areas that require more attention before formal design. Resource allocation is critical for custom projects.
We have collected many best practices that have streamlined our process for technical custom-building projects:
- Establish client needs: Before circulating drawings and quotes with the team, it’s crucial to establish needs for parameters like occupancy, compliance, size restrictions, fire ratings, area classifications and basic design elements. Understanding local and state codes is also vital to guiding a new project design. Inappropriate initial concepts can derail budget and design efforts.
- Scope of work (SOW): A well-designed initial concept, based on end user needs, evolves into drawings that spark discussions and refinements. This SOW should include project team and peer reviews to avoid oversights. This guides the project, setting clear expectations for all tasks.
- Cross-departmental collaboration: Ensure project team members handling electrical, plumbing, mechanical and masonry are aware of their own and their colleagues’ responsibilities. This is vital for large custom projects. Complex change orders arise when multiple trades share a common issue, impacting both owner and builder.
- Leverage site visits: While experts can foresee issues from topographical drawings, site visits almost always expose something not seen on the drawing, like an overhead obstacle, drainage concerns, insufficient crane space and others. Onsite assessments offer insights that technology alone cannot provide.
- Collaboration during estimating: Designers often rely on estimators to make substantial assumptions, which leads to errors. Estimating errors lead to difficult conversations later. Collaborating during the estimating phase identifies potential change orders early.
- Prioritize constructability reviews: A brief constructability review before project commitment often prevents change orders. A 15-minute call between project stakeholders and members of the drafting, estimating and project management teams usually brings up last-minute changes that save both time and money.
- Identify historical changes: Reviewing old project files, past challenges and tapping into project managers (PMs) who aren’t typically involved in the design or estimating phase can avert change orders. I recall an early project with a particular customer who requested late-phase IT changes. Now, reviewing previous IT installations with this client helps incorporate these specs upfront, preventing another change order.
- Involve PMs and internal subject matter experts early: Engaging project managers and internal experts during estimating can improve your SOW since they have knowledge in their fields and valuable vendor contacts. Even in firms where PMs aren’t part of bidding, their input can align end users and contractors.
These are just a few of the practices RedGuard uses in completing custom projects that successfully avoid costly change orders.
For more information, visit redguard.com or call (855) 733-4827.
Bryan Bulling
Bryan Bulling is a Regional Area Manager for RedGuard, serving the Northeastern United States. He's an expert in the areas of hazard consultations and blast-resistant solutions. He has more than thirty years of experience in a range of industries, some of those include construction, industrial/commercial architecture, oil and gas refining, and project planning.