Articles | Best Practices | Turnarounds
Effective Project Management Ensures Smooth Turnarounds
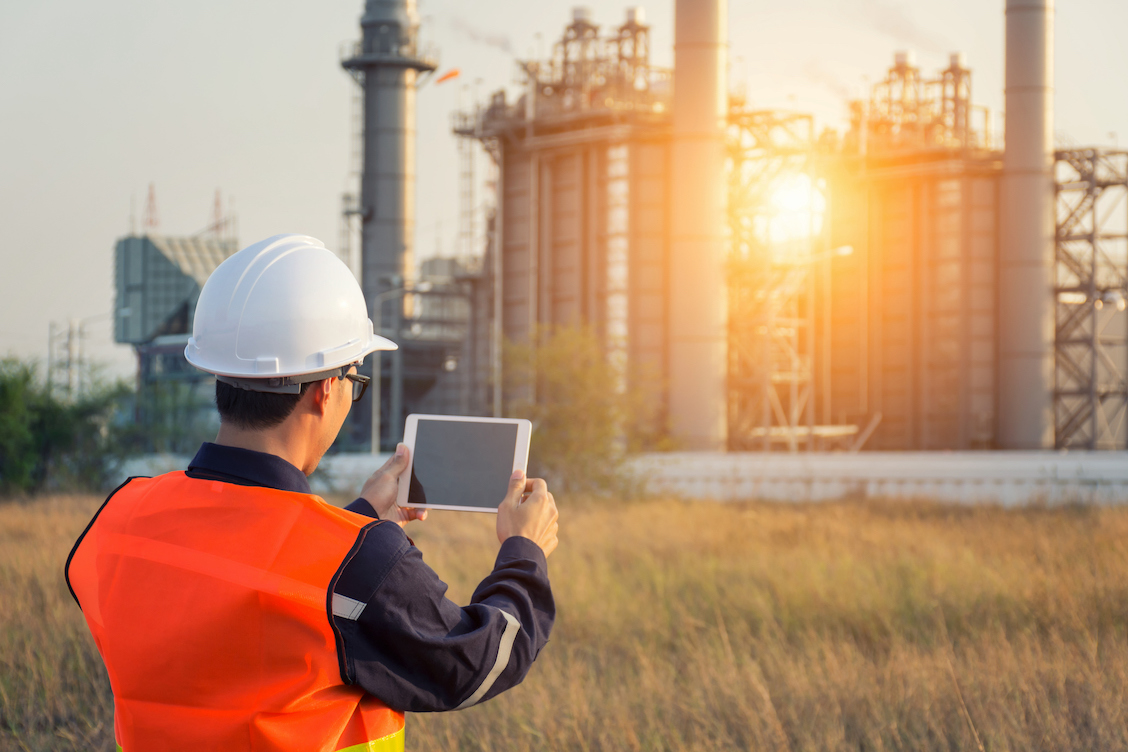

This article was originally published in the May/June 2021 issue of BIC Magazine. It is republished here in its entirety and includes an opportunity to schedule a meeting with the writer.
Have you ever pulled up to a gas pump and stepped out of your car only to realize your gas cap is on the other side? How frustrating. Now imagine you are pulling into a congested petrochemical plant driving a flatbed tractor-trailer. You are carrying a very heavy blast-resistant module on the back. At some point, you realize the doors are on the wrong side for roll-off delivery. That’s frustrating for you and your customer.
With the largest fleet of rental blast-resistant modules in the world, RedGuard has learned a few things about organizing for large turnarounds. Here’s how we do it.
It starts with our knowledgeable direct sales team being in contact with the facility turnaround team months in advance. Open communication ensures that needs are understood and prepares RedGuard and the client for the requirements. The entire RedGuard team needs to understand the types and quantities of blast-resistant modules needed and critical move-in and move-out dates. They need to know exactly where the modules are going and what orientation is required. The local RedGuard direct salesperson is the liaison between the client and all departments at RedGuard.
The logistics team will ensure the blast-resistant modules arrive on time and in the types and quantities promised. Based on information from the site, the team will decide to deliver with roll-off trailers or flatbed trailers. The award-winning team of transportation specialists from RedGuard will need to know site access and safety rules. With the largest company-owned fleet of delivery trucks for blast resistant modules and the most advanced and efficient logistics team in the industry, we do our best to provide seamless move-in and move-out.
If multi-sectional buildings or stacked buildings are required, a site assembly team is necessary. All members of the assembly team need the proper credentials and safety training, and the manufacturer must have the appropriate safety ratings to allow its team to work at the site. The manufacturer and its team must fully understand the client’s schedule and develop a plan to meet it. Even for a large number of single units, safety is a crucial factor in the mobilization process. Besides being familiar with the site safety requirements, there is an inherent danger in moving large, heavy modular buildings. In this case, experience matters. RedGuard drivers and service personnel are the safest and most experienced in the industry, and our safety statistics and awards back that up.
About two years ago, RedGuard saw a need and introduced free project managers to assist with some of the industry’s more extensive turnarounds. This key position not only coordinates RedGuard’s delivery and installation but also ensures the client is ready with a clear path to the site, power and other services in place, and a clear and reasonable schedule for delivery and pickup. It may sound expensive to offer this free service, but the project managers have quickly paid for themselves many times over by avoiding poorly timed or improperly loaded (like the gas cap) deliveries. They also shorten the overall time for delivery and removal by ensuring everyone is on the same page.
Offshore project coordination is just as critical. Our offshore division, Specialist Services RedGuard, often mobilizes large quantities of accommodation units, galley/diner modules, support modules, hazardous area office and workshop modules. Whether for offshore service vessels or installation on actual offshore rigs, time is of the essence. Installations can involve stacking dozens of modules in an orderly and safe manner.
Coordination by logistics, field installation, and project management personnel is required to meet a vessel at the right time and get things installed safely and quickly. After all, service vessels don’t make money sitting in port.
Installation on offshore rigs must be planned far in advance. This includes sending tools out on a boat long before the service technician leaves to ensure the tools arrive before the technician and stocking it with all the tools necessary to perform the work and handle any other issues that may arise.
Good project management isn’t anything new in capital projects. Still, in the case of sizeable modular building mobilizations and demobilizations, it can be just as critical to project safety, budget and schedule. At RedGuard and Specialist Services RedGuard, we realize the importance of good project management and put the resources in place to ensure it.
For more information, set up a meeting with the author, RedGuard's Market Development Manager, Dean Alcott.
Dean Alcott
Dean is the Market Development Manager for RedGuard and he has more than 25 years of experience with specialty modular structures. He has been heavily involved in transforming RedGuard from company that did business only in North America, to a global leader in the manufacture and supply of safe space.