Safety & Regulations | Design & Engineering
Concrete & Condensation in Blast-Resistant Buildings
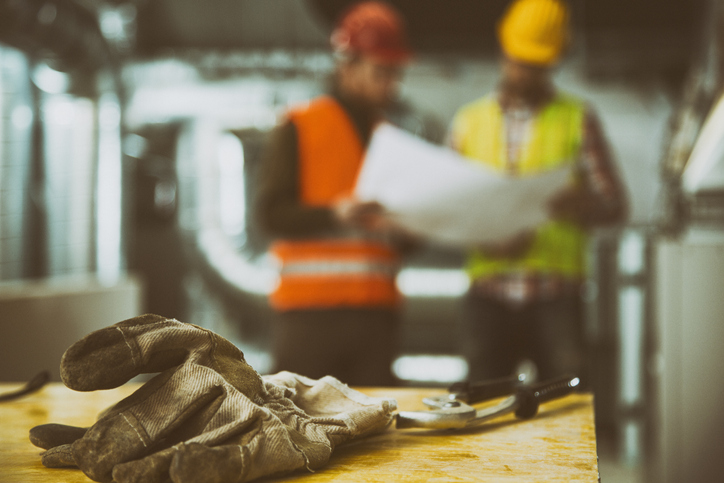

Dealing with moisture is inevitable in most places. Humidity and rain can cause condensation inside and outside buildings, allowing moisture to seep up from the ground. Moisture can come from leaky fixtures or overzealous HVAC units, even in dry areas.
Condensation occurs when warm air comes in contact with cold surfaces, and it can be a significant factor in choosing a building material. Lumber, for example, retains water efficiently. Concrete can also be highly affected by condensation. It doesn’t take much moisture to penetrate concrete, pushing apart the grains and affecting strength and durability.
This is a reason to consider the safety of steel over concrete in the construction of blast-resistant buildings.
The Dangers Of Condensation For Buildings
When moisture enters concrete, the concrete expands, deforming the material. It can also cause spalling, which is when concrete cracks, flakes, apart, or separates from other building materials. The resulting structural damage can be catastrophic.
When moisture condenses and sits on building materials, it can also lead to mold growth and other volatile organic compounds (VOCs). This growth can cause the deterioration of plaster and paint and cause health problems for anyone who works in a damp building. Even in metal buildings, condensation can lead to rust, corrosion, the growth of mold, and the reduction of indoor air quality.
Recent events have shown us the dangers of reinforced concrete buildings and the loss of life resulting from uncontrolled condensation. And it’s just one more reason why you want a building that’s designed to be blast-resistant to be built using a material like steel.
Condensation Catastrophes
We often assume that we’ll know if moisture has seeped into a building, but many of the telltale signs are invisible. For example, interstitial condensation occurs within enclosed walls, roofs, or floor cavities, leaving a concrete building structurally unsound without tenants knowing about it. That’s one of the reasons buildings require inspection and follow-up.
Sadly, we’ve recently seen just how much damage moisture condensation can do to a reinforced concrete building when the Champlain Towers South apartment complex in Surfside, Florida, near Miami, collapsed in early 2021. This tragedy could have been avoided, but instead, 98 people lost their lives.
Some evidence suggests that moisture from the structure’s pool penetrated the concrete and corroded the rebar meant to reinforce it. There are also records showing that a consultant found significant structural damage to the concrete slab below the pool deck and cracking and crumbling of the columns, beams, and walls of the parking garage back in 2018. A memo noted that water was seeping up “from the underground as a result of storm surge.”
However, even waterproof concrete does not last forever. At Champlain Towers South, a core sample of the concrete taken in 2020 showed no signs of the original waterproofing and found that the concrete was crumbling away from the steel rebar meant to strengthen it.
Of course, reinforced concrete is a common building material used for blast-resistant design, so it’s reasonable to be concerned that moisture might affect a building’s ability to protect occupants, at a minimum. This is especially relevant considering that many oil & gas industry locations are in warm, humid, coastal areas where condensation is present. Construction was going on next door to the complex, resulting in vibrations. If that was, indeed, a contributing factor, it’s still far less pressure than a blast-resistant building would be expected to take.
Reasons To Rely On Steel For Your Blast-Resistant Building
Since concrete can fail on its own due to condensation even without a blast, steel is the safer alternative.
While all buildings can potentially have condensation issues, there are steps a reliable company will take to ensure that a steel blast-resistant building maintains its integrity. These include:
- Adding proper insulation to regulate internal temperature
- The installation of vapor barriers and interior ventilation
- Checking the concrete foundation for potential problems before the building is placed on top
A good building company makes a huge difference. Take the time to carefully select a trustworthy company that offers on-site services such as risk assessments and a long-term service agreement. After all, it could be a matter of life or death.
RedGuard Sales & Marketing
The RedGuard sales and marketing team curates and writes on a variety of topics regarding blast-resistance and modular buildings. To inquire about any of the topics you read about on our blog, connect with us.