Best Practices | Safety and Regulations
How to Prepare for Potential Oil Refinery Explosions
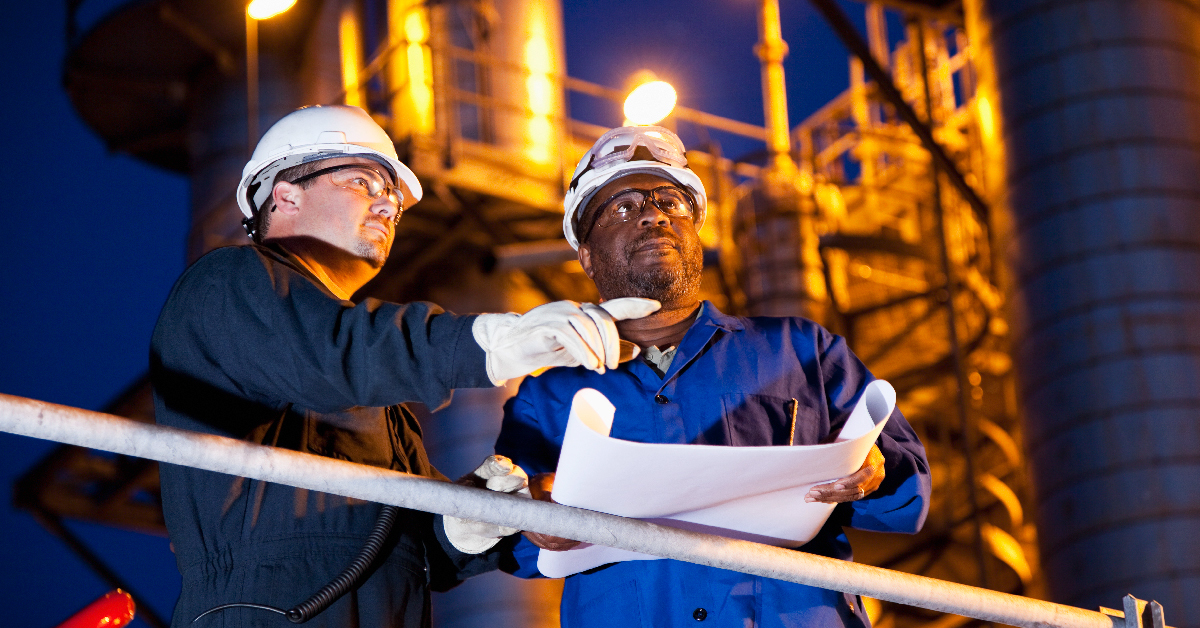

One of the most devastating petrochemical plant explosions in U.S. history occurred in 1989 when a petrochemical complex experienced a polyethylene leak, resulting in a flammable vapor cloud. Sometime after lunch, the cloud was ignited, causing a series of explosions and fires that killed 23 workers and injured over 130 more.
While explosions at petrochemical facilities are relatively rare, they do occur and are often devastating. Below, we'll look at how a proper hazard prevention strategy, including the installation of blast resistant buildings, can help these facilities stay safe.Employer Responsibility
Owners of petrochemical facilities in the U.S. must abide by Process Safety Management (PSM) regulations issued by OSHA. OSHA 1910.119 (Process Safety Management of Highly Hazardous Chemicals) lays out the guidelines for developing the PSM program and consequences for those who don't follow these guidelines, therefore jeopardizing the health and lives of employees, contractors, visitors, and those who live near a facility.
To stay up-to-date with regulations, employers in the petrochemical industry need to:
- Identify experienced employees to lead facility operations
- Document all hazardous chemicals and make them known to employees
- Perform a Process Hazard Analysis every five years to analyze the safety of the site and the protocols in place
- Update PHA data whenever new elements are installed
- Lay out the operating procedures for all equipment
- Train employees on these procedures as well as on all safety protocols
- Consistently evaluate contractor safety
- Perform and document routine inspections on the site and all of its equipment
- Carefully document all changes in procedures and equipment
- Perform incident investigations
- Develop emergency response plans
Process safety failures are at the root of most petrochemical plant explosions. The most common causes of these failures across all industries include shortcomings related to:
- Procedures
- Training
- Emergency preparedness
- Hazard identification
- Process safety management
Step 1: Re-Examine Safety Protocols for Each Step of the Process
There is a clear need for petrochemical facilities to regularly examine and update safety protocols to protect workers from exposure to toxic chemicals. Optimal safety begins before a plant is designed. It continues through the development of processes, the hiring of personnel, and every phase of growth after that.
But as technology improves and we learn more from past mistakes, every aspect of petrochemical plant design and management needs to be periodically reassessed to ensure facilities meet safety requirements and give employees the peace of mind they need to do their jobs well.
The leadership on safety needs to be a priority, starting from the top of the management chain as companies make visible commitments to optimal operating procedures. Not only do companies need to focus on the safety of current processes, but they also need to enhance and update them when necessary and examine industry incidents to ensure past mistakes aren't repeated.
Step 2: Implement Changes in Protocol if Needed
As technology evolves, so do the safety protocols needed to operate it. New technology also gives us new tools to enhance safety, including backup mechanisms, early warnings, or new materials for better protective equipment.
Petrochemical facilities must implement safety protocol changes when they update their processes and equipment. But revisiting current protocols, especially in light of any safety incidents that have occurred (at any similar facility), is the best way to enhance worker safety.
A Job Hazard Analysis (JHA) is a standard approach to minimizing risks. During a JHA, safety managers will break down tasks into smaller steps, identify any potential hazards along each step of the process, and identify preventative measures to control those risks.
Of course, written safety rules aren't enough. Workers have to be adequately trained to follow protocols.
Step 3: Train and Refresh Team on Safety Protocols
Creating a safety culture at petrochemical facilities requires consistent training on all updates and refresher sessions to avoid complacency. Involving employees in the hazard identification as well as the implementation of new safety measures helps ensure maximum compliance.
It takes practice (in the form of demonstrations and drills, for example) to ensure employees are adept at reacting to the unexpected. That's why some facilities use safety software, including mobile apps, to keep track of safety audits and checklists for new guidelines. Others rely on more comprehensive safety training programs. RedGuard uses SafeStart, a safety program focused on human error prevention.
Step 4: Utilize Blast Resistant Buildings
If disaster strikes, even the best safety protocol won't be enough unless a facility has protective equipment to shield workers from chemical leaks and blasts, including any resulting debris or fire-related hazards. That's why blast resistant buildings are a necessary safety feature for petrochemical facilities.
However, not all blast resistant buildings are created equal, and chemical facilities have unique needs. First, it's critical to choose a building based on its ability to withstand a blast and any resulting flash fires. Steel structures are the best choice since they're designed to withstand the shockwave of an explosion. Steel has the ductility and tensile strength ideal for blast resistance and can withstand the pressure of a blast of up to 9.9 psi.
The ability to install a blast resistant building on a job site with minimal disruption is also crucial. At RedGuard, our modular buildings are constructed off-site to an individual company's needs and assembled in a fraction of the time it would take to build a permanent concrete structure.
RedGuard's buildings have also been blast-tested by third-party engineers to ensure they can withstand the pressure and keep people safe. When lives are on the line, companies need proof that their safety investments will pay off. That's one of the reasons RedGuard uses third-party engineers to test our designs objectively.
Protecting the Petrochemical Industry
Petrochemical plants stand to lose a lot when blasts occur, but nothing more precious than human lives. Luckily, many of these events can be prevented by enhancing safety protocols and training employees to take them seriously and react with care. But when accidents do ensue, it's crucial to have steel blast resistant buildings on site to wait out the worst of an incident.
RedGuard's customizable, steel blast resistant buildings are ideal for petrochemical facilities because they are built off-site and come with the peace of mind provided by blast testing.
If you're interested in learning more about how to keep your workers safe on site, speak with our expert team to learn more.
RedGuard Sales & Marketing
The RedGuard sales and marketing team curates and writes on a variety of topics regarding blast-resistance and modular buildings. To inquire about any of the topics you read about on our blog, connect with us.