Best Practices | Design & Engineering
Exterior Elements of Blast-resistant Buildings
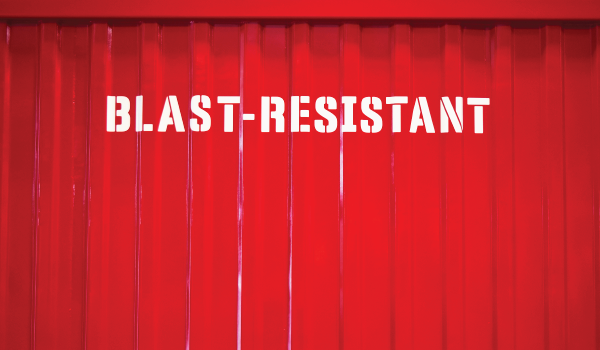

This article was originally published in the September 2020 issue of BIC magazine, but was edited for brevity. It is published here in its entirety. It was written by Bryan Bulling, one of RedGuard's subject matter experts and our Northeast Regional Area Manager.
As the summer of 2020 winds down and transitions into fall, let’s take some time to learn more about modular blast-resistant buildings. While the exteriors of blast-resistant buildings are typically simple and utilitarian and are often mistaken for shipping containers, there are many unique exterior elements upon closer examination that deliver serious functionality and purpose.
Corrugated Steel
Perhaps the most identifiable aesthetic of a blast-resistant building is its thick, corrugated steel exterior. With corrugation ridges running vertically, the steel exterior cladding of the building works with an engineered structure, or frame, beneath to create the primary protection around blast-resistant design. While steel has excellent tensile strength, its compressive strength is relatively weaker. Corrugation increases rigidness and strength, which subsequently improves protection.
Exterior Coatings
Facilities in our industry can be located in very harsh and extreme climates. Additionally, the environment within and around facilities can present factors that greatly affect component finishes. To prevent corrosion, many blast-resistant building manufacturers utilize a protective exterior coating, typically part of an installation process that includes sand-blasting, treatment, priming, and one or more coats of a final finish. This finish minimizes corrosion over the life of the building. Heavy industrial coatings like polyurea, polyurethane, and other high strength coatings are ideal. A benefit of these types of coatings is that when bumped, scraped, or gouged, blemishes on a blast-resistant building can be ground out, treated, primed, and recoated inexpensively, which is not as easy on a typical masonry or stick-built structure.
Roofline
To a casual observer, a blast-resistant building’s roof appears to be flat. However, behind the horizontal ridgeline where the apparent roof meets the vertical walls, there is a sloped panel roof surface that diverts water to one or two sides of the structure. The best designs seek to minimize diversion of water to seams where individual building modules join or to areas of the roof that have penetrations. It is not uncommon for manufacturers to utilize some form of waterproofing membrane, coating, or covers on blast-resistant buildings to improve resistance against water infiltration.
ISO Connections
One of the primary benefits of a modular blast-resistant building is the ability to be lifted, transported, moved efficiently. Nearly all will include highly visible ISO lifting elements, allowing for safe and efficient delivery anywhere in the world. ISO design allows a blast-resistant module to be handled by all types of cranes, top loaders, straddle carriers, reach stackers, and tilt beds. Additionally, some manufacturers, including RedGuard, implement fork pockets on the base, which allow side-picking and lifting by suitable forklifts. The wide range of options available for moving a blast-resistant building allows for transport via truck, boat, train, or even helicopter!
Blast-Resistant Windows
Typically, a blast-resistant building is primarily designed for protection, with comfort and amenities secondary. However, in recent years, improved design processes and the availability of high-strength blast-resistant glass have enabled manufacturers to install windows in blast-resistant buildings, which vastly improve functionality of modules used for control, security, and offices. These windows are fixed, ideally minimally sized, and engineered to match or exceed the building’s hazard rating (an 8 psi building with a 5 psi window will be rated overall at 5 psi).
Placards
Given the mobile nature of a modular blast-resistant building, it is likely that a unit will someday be moved after being delivered to a site. RedGuard includes numerous placards on every building identifying the building’s hazard rating. This ensures proper siting in the future, correctly matching a building’s hazard rating with an active hazard area if it’s being relocated.
Internal Fixtures
While there are not a lot of exterior fixtures found on a typical blast-resistant building, there are overhead door lights, electrical disconnects, HVAC components, and communications equipment. Typically, blast-resistant fixtures are carefully specified in design, so that these more robust fixtures don’t become projectiles during an explosion. Additionally, the site’s area electrical classification will drive component specifications, as the presence of combustible gases and possible sources of ignition are addressed.
HVAC
On large, multi-section installations, an HVAC is most efficiently installed as a pad-mounted unit, with common ducting distributing heat/cool air throughout the blast-resistant building. However, most blast-resistant buildings will have an HVAC system – typically reverse hot and cold – mounted somewhere on the building’s exterior. Typically prewired to the unit’s service panel, an exterior-mounted HVAC system is efficient, easy to use, and highly serviceable. There are many variations of wall-mounted HVAC systems available, including blast-resistant, high efficiency, special-use in classified areas, corrosion-resistant, etc.
Air Stack
One last exterior element worth mentioning, due to increasing popularity, is a fresh air intake stack. For use in hazardous areas where potentially toxic gases are present, a blast-resistant building equipped with a positively pressurized interior atmosphere will draw fresh air from a 12’+ stack that rises above the potential cloud of hazardous gases. This protects occupants inside the blast-resistant building from being exposed to those gases.
If you, or someone on your site, would like to understand how to address hazards through the use of blast-resistant buildings, feel free to use me as a resource or to start a discussion. Meetings can be scheduled through the link below.
Bryan Bulling
Bryan Bulling is a Regional Area Manager for RedGuard, serving the Northeastern United States. He's an expert in the areas of hazard consultations and blast-resistant solutions. He has more than thirty years of experience in a range of industries, some of those include construction, industrial/commercial architecture, oil and gas refining, and project planning.