Designing Blast-Resistant Buildings (That Actually Save Lives)
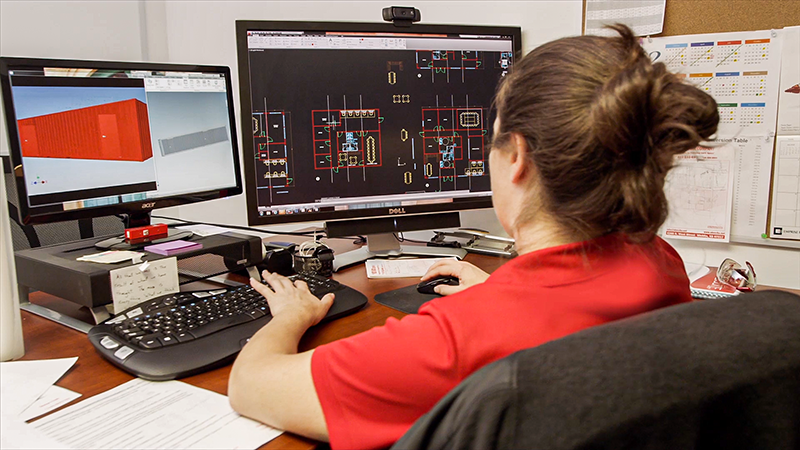

In 2005, my team was called in to investigate the Texas City, Texas, refinery disaster. I’ll never forget what I saw there — where wood-frame office trailers had stood, only splinters remained. Fifteen people died because they were housed in those trailers. All I could think was there has to be a better way.
Around the same time, ConocoPhillips approached RedGuard, a Kansas-based company that had been supplying ConocoPhillips with ground-level offices, to ask if the company could build a more rugged office design to protect personnel in a blast zone. RedGuard contacted me, and we set out on a mission to save lives.
A new way of thinking
At first, we tackled the idea as any structural engineer would: erect a rectangular framework, add some walls and anchor it to a foundation. This had flaws as traditional buildings aren't designed to withstand explosive forces.
Then someone suggested retrofitting a shipping container as our basic framework. This had merit; containers were in heavy use all over the world, which kept costs down, even on the brand-new units they ended up using. It also simplified the design process because a container’s steel construction made it more blast proof than a traditional building — even before adding reinforcement.
Furthermore, I had seen shipping containers in the blast zone at Texas City — still standing among the splinters of wood-frame buildings. I knew we were onto something.
This approach also had exciting possibilities in terms of portability, representing a huge advantage for offshore platforms. We knew a container-based building would be cheaper to transport and easier to set up than the concrete and cinder block structures in common use. It also occurred to us several containers could be combined to make a larger space, which has since proven practical. Even onshore facilities would benefit from portability, we knew, when work flows change or facilities expand, and buildings need to be moved. (RedGuard now constructs all buildings from scratch, based on the container design and is also custom fabricating permanent blast-resistant buildings, based on the same principles, but that’s too big a story to tell here.)
A new way of building
There were other companies selling blast-resistant buildings, so our first step was to research their products. I noticed no testing had been done on these designs, so no one really knew how they would stand up in a blast zone. The second thing that struck me was even more alarming — every blast-resistant building on the market was designed to hold together as a structure but with little attention to protecting the personnel inside. I was amazed to learn some petrochemical plants were buying them based on interior amenities like attractive lighting fixtures and even glass mirrors in the restrooms, which could injure or kill personnel in a blast. This is still true of many blast resistant buildings being sold today.
My third concern arose from the fact other blast-resistant buildings were designed like traditional metal buildings, with very little data gathered to determine how they would actually respond to an explosion. As we performed failure analysis, it was obvious our container-based design was much stronger, and as it turned out, lower in cost.
The all-important testing process
We designed, built and then did something unprecedented in the field of blast resistant buildings — we tested them. If you like to watch Hollywood-quality explosions, click on the blast test video. They speak for themselves, in terms of the product’s ability to survive close-proximity explosions.
What you don’t see in these videos is the most important part of the process. When we tested, we didn't just use empty containers. We added lights, furniture, computers and test dummies. Nobody else has done this, to this day, but we needed to be confident our product could actually save lives. It can. Hopefully there will never be an opportunity to find out how they perform in a real disaster, but if I’m ever close enough to witness an explosion at a refinery or chemical plant, I know where I want to be.
Dr. Ali Sari
Dr. Sari has more than 20 years of experience in the analysis of Onshore and Offshore structures. He has professional experience in dynamic analysis and design of Onshore and Offshore structures and equipment to resist blast loads from high explosives and vapor cloud explosions.